Pipe bus connector
A connector and tube busbar technology, applied in the direction of connecting contact material, welding/welding connection, clamping/spring connection, etc., can solve the problem of loosening of tube busbar and open conductive metal sleeve, affecting the insulation effect of shielding insulating layer, and smooth surface. It can easily shield the insulation treatment, meet the high current transmission, and improve the safety factor.
- Summary
- Abstract
- Description
- Claims
- Application Information
AI Technical Summary
Problems solved by technology
Method used
Image
Examples
Embodiment 1
[0025] Such as figure 2 As shown, a conductive sleeve 2 matching the outer diameter of the copper bus conductor 3 is placed at the connecting part of the two copper bus bars. The material of the conductive sleeve 2 is the same as that of the copper bus conductor 3. The corresponding positions of the bus conductors 3 are welded with the same material of solder, and then the opening 1 of the axial opening 1 of the conductive sleeve 2 is welded with the solder of the same material as the copper bus conductor 3, so that the connecting part of the copper bus is closely connected with the conductive sleeve 2 Connect as one. Finally, the welding joint shall be polished and smoothed, and then shielded and insulated.
Embodiment 2
[0027] Such as figure 2 As shown, a conductive sleeve 2 matching the outer diameter of the aluminum bus conductor 3 is placed at the connecting part of the two aluminum busbars. The material of the conductive sleeve 2 is the same as that of the aluminum busbar conductor 3. The solder of the same material is used for welding between the corresponding positions of the bus conductor 3, and then the opening 1 of the axial opening 1 of the conductive sleeve 2 is welded with the same material as that of the aluminum bus conductor 3, so that the connecting part of the aluminum bus is closely connected with the conductive sleeve 2 Connect as one. Finally, the welding joint is polished and smoothed, and then shielded and insulated.
Embodiment 3
[0029] Such as figure 2 As shown, the conductive sleeve 2 matching the outer diameter of the alloy bus conductor 3 is placed at the connecting part of the two alloy bus bars for large current. The material of the conductive sleeve 2 is the same as that of the alloy bus conductor 3. The conductive sleeve 2 The solder of the same material is used for welding between the two end edges of the alloy bus conductor 3 and the corresponding positions of the alloy bus conductor 3 . , and then weld the opening 1 at the axial opening 1 of the conductive sleeve 2 with the same material as the alloy busbar conductor 3, so that the connecting part of the alloy busbar and the conductive sleeve 2 are tightly connected as a whole. Finally, the welding joint is polished and smoothed, and then shielded and insulated.
PUM
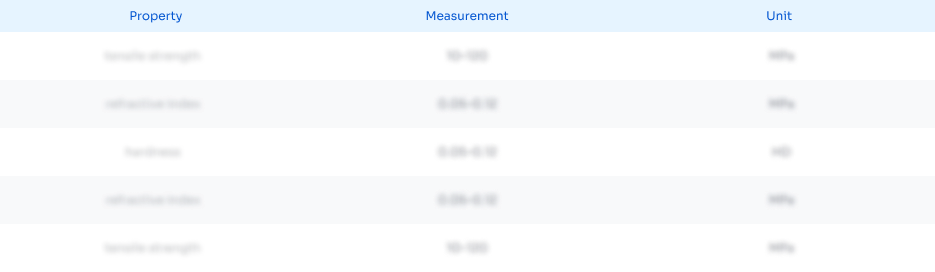
Abstract
Description
Claims
Application Information

- R&D
- Intellectual Property
- Life Sciences
- Materials
- Tech Scout
- Unparalleled Data Quality
- Higher Quality Content
- 60% Fewer Hallucinations
Browse by: Latest US Patents, China's latest patents, Technical Efficacy Thesaurus, Application Domain, Technology Topic, Popular Technical Reports.
© 2025 PatSnap. All rights reserved.Legal|Privacy policy|Modern Slavery Act Transparency Statement|Sitemap|About US| Contact US: help@patsnap.com