Vacuum glue-dipping insulation pipe without air gaps and manufacturing method thereof
A manufacturing method and technology of insulating tubes, applied in the direction of insulators, insulators, electrical components, etc., can solve the problems of poor electrical and mechanical properties of insulating tubes, and achieve the effect of improving electrical and mechanical properties
- Summary
- Abstract
- Description
- Claims
- Application Information
AI Technical Summary
Problems solved by technology
Method used
Examples
specific Embodiment approach 1
[0007] Specific embodiment one: The insulating tube of this embodiment is wound by glass cloth, and the resin glue is impregnated in the glass cloth, and described resin glue is made of 100 parts of epoxy resin, 85 parts of curing agent, 10 parts by weight. 3 parts of toughening agent and 3 parts of accelerator are stirred at a temperature of 50-80°C. Traditional insulating tube manufacturing methods can only process insulating tubes with circular cross-sections; the insulating tubes in this specific embodiment can be wound into circular, rectangular or elliptical cross-sections.
specific Embodiment approach 2
[0008] Embodiment 2: The curing agent in this embodiment is methyl tetrahydrophthalic anhydride or methyl hexahydrophthalic anhydride. Methyltetrahydrophthalic anhydride or methylhexahydrophthalic anhydride has low viscosity and good penetrability. Other compositions are the same as in Embodiment 1.
specific Embodiment approach 3
[0009] Embodiment 3: The toughening agent in this embodiment is polynonyl dianhydride. Polynonyl dianhydride has good toughness effect. Other compositions are the same as in Embodiment 1.
PUM
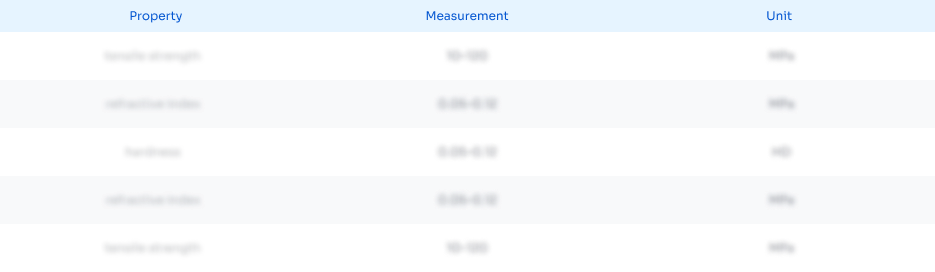
Abstract
Description
Claims
Application Information

- R&D
- Intellectual Property
- Life Sciences
- Materials
- Tech Scout
- Unparalleled Data Quality
- Higher Quality Content
- 60% Fewer Hallucinations
Browse by: Latest US Patents, China's latest patents, Technical Efficacy Thesaurus, Application Domain, Technology Topic, Popular Technical Reports.
© 2025 PatSnap. All rights reserved.Legal|Privacy policy|Modern Slavery Act Transparency Statement|Sitemap|About US| Contact US: help@patsnap.com