High refractivity resin lens and preparation method thereof
A resin lens, high refractive index technology, used in optics, instruments, optical components, etc., can solve the problems of low refractive index, unsatisfactory comprehensive performance, limited application scope of materials, etc., to achieve a wide range of applications and improved comprehensive performance. Effect
- Summary
- Abstract
- Description
- Claims
- Application Information
AI Technical Summary
Problems solved by technology
Method used
Image
Examples
Embodiment 1
[0027] The first step of synthesis of thioglycerol (SR1)
[0028] Add 0.05 mol of 1,2,3-trichloropropane, 0.3 mol of thiourea and 0.35 mol of concentrated hydrochloric acid into a 100 mL three-necked flask equipped with electromagnetic stirring, a thermometer, and a reflux condenser, heat and reflux for 24 hours, then cool After reaching room temperature, add 0.4 mol of ammonia water, slowly raise the temperature to 60°C, heat and stir for 5 hours, then stand for stratification, remove the upper aqueous solution, pickle the lower layer, wash with water, and distill to obtain the product SR1;
[0029] Preparation of the second step high refractive index resin lens
[0030] Mix SR1 and isocyanate compound evenly at a molar ratio of 1:1, then add 0.5% of the total mass of the mixture as a phosphate-based internal mold release agent and 0.05% of the total mass of the mixture as an organotin catalyst, and then follow the instructions for synthetic resin lenses. The standard requir...
Embodiment 2
[0034]Synthesis of the first step benzenedimethanol (SR2)
[0035] Add 0.05 mol of benzenedimethanol, 0.15 mol of thiourea and 0.2 mol of concentrated hydrochloric acid into a 100 mL three-necked flask equipped with electromagnetic stirring, a thermometer, and a reflux condenser, heat and reflux for 30 hours, then cool to room temperature, and then add 0.2 mol of ammonia water, slowly warming up to 65°C, heating and stirring for 4 hours, standing for stratification, removing the upper aqueous solution, pickling the lower layer, washing with water, and distilling to obtain the product SR2;
[0036] Preparation of the second step high refractive index resin lens
[0037] Mix SR2 and isocyanate compound uniformly at a molar ratio of 1.2:1, then add 0.5% of the total mass of the mixture as a phosphate-based internal mold release agent and 0.05% of the total mass of an organotin catalyst, first at 50-60°C After vacuum defoaming and prepolymerization for 2 hours, inject it into the...
Embodiment 3
[0042] The first step 2,3-dimercaptopropylthiopropanethiol (SR4)
[0043] Add 0.01mol of mercaptoethanol and 0.015mol of pyridine into a 100mL three-necked flask equipped with electromagnetic stirring, a thermometer, a reflux condenser and a dropping funnel, and then add 0.005mol of epichlorohydrin dropwise at 35°C. Then continue to react for 1 hour, add 0.1 mol of thiourea and 0.15 mol of concentrated hydrochloric acid, heat and reflux and stir for 12 hours, then cool to room temperature, add 0.25 mol of ammonia water, slowly raise the temperature to 60 ° C, heat and stir for 4 hours, and then let stand to separate Layer, after the upper aqueous solution is separated, the lower layer is pickled, washed with water, and the product SR4 is obtained after distillation;
[0044] Preparation of the second step high refractive index resin lens
[0045] Mix SR4 and isocyanate compound evenly at a molar ratio of 0.8:1, then add 0.5% of the total mass of a phosphate-based internal mol...
PUM
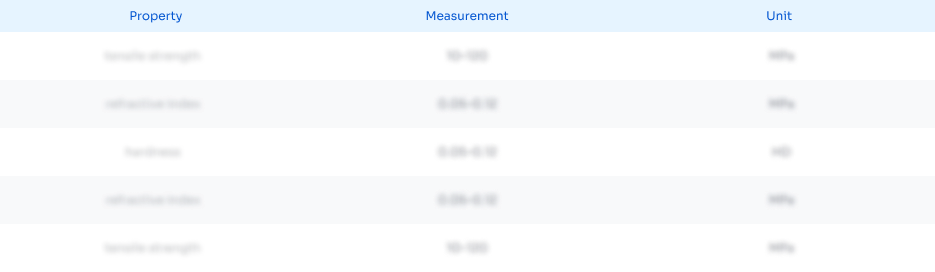
Abstract
Description
Claims
Application Information

- Generate Ideas
- Intellectual Property
- Life Sciences
- Materials
- Tech Scout
- Unparalleled Data Quality
- Higher Quality Content
- 60% Fewer Hallucinations
Browse by: Latest US Patents, China's latest patents, Technical Efficacy Thesaurus, Application Domain, Technology Topic, Popular Technical Reports.
© 2025 PatSnap. All rights reserved.Legal|Privacy policy|Modern Slavery Act Transparency Statement|Sitemap|About US| Contact US: help@patsnap.com