Dry surface modification method for electronic grade super-fine silicon micro-powder
A surface modification, ultra-fine silicon technology, applied in the direction of dyeing organosilicon compound treatment, fibrous fillers, etc., can solve the problems of large specific surface area, high surface energy, easy agglomeration, etc., to improve compatibility and improve bonding force , The effect of good arc resistance
- Summary
- Abstract
- Description
- Claims
- Application Information
AI Technical Summary
Problems solved by technology
Method used
Examples
Embodiment 1
[0015] Example 1. A dry surface modification method of electronic grade ultrafine silica powder, the steps are as follows:
[0016] (1) Select ultrafine silica powder with D50=3-50 μm as raw material;
[0017] (2) Prepare surface modification mixed liquid; described surface modified mixed liquid is made up of the raw material of following weight ratio: silane coupling agent 80%; Silane surfactant 12%; Macromolecular hyperdispersant 8%;
[0018] (3) After heating the raw material to 80°C, add 0.3% surface modification mixed liquid to the raw material to coat and modify the raw material, keep it warm for 30 minutes, discharge and cool the raw material to obtain the finished product.
Embodiment 2
[0019] Example 2. A dry surface modification method of electronic grade ultrafine silica powder, the steps are as follows:
[0020] (1) Select ultrafine silica powder with D50=3-50 μm as raw material;
[0021] (2) preparing a surface modification mixed solution; the surface modified mixed solution is made of the following raw materials in weight ratio: 90% of silane coupling agent; 6% of silane surfactant; 4% of polymer hyperdispersant;
[0022] (3) After heating the raw material to 145° C., adding 3.0% of the surface modification mixed liquid to the raw material by weight, coating and modifying the raw material, keeping the temperature for 120 minutes, and then discharging and cooling to obtain the obtained product.
Embodiment 3
[0023] Example 3. A dry surface modification method of electronic grade ultrafine silica powder, the steps are as follows:
[0024] (1) Select ultrafine silica powder with D50=3-50 μm as raw material;
[0025] (2) Prepare surface modification mixed liquid; described surface modified mixed liquid is made up of the raw material of following weight ratio: 88% of silane coupling agent; 10% of silane surfactant; 2% of macromolecular hyperdispersant;
[0026] (3) After heating the raw material to 130° C., adding 1.5% of the surface modification mixed liquid to the raw material by weight, coating and modifying the raw material, keeping the material warm for 60 minutes, and then discharging and cooling to obtain the finished product.
PUM
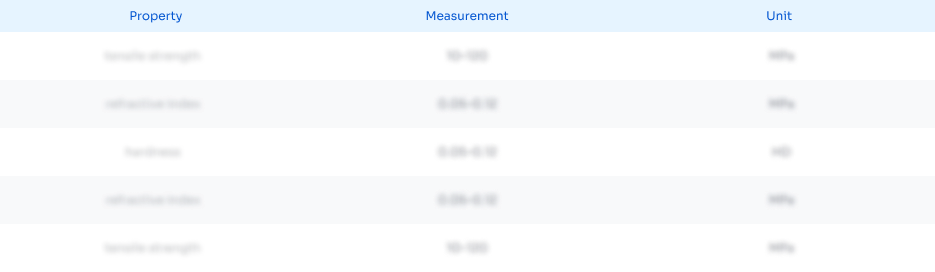
Abstract
Description
Claims
Application Information

- R&D
- Intellectual Property
- Life Sciences
- Materials
- Tech Scout
- Unparalleled Data Quality
- Higher Quality Content
- 60% Fewer Hallucinations
Browse by: Latest US Patents, China's latest patents, Technical Efficacy Thesaurus, Application Domain, Technology Topic, Popular Technical Reports.
© 2025 PatSnap. All rights reserved.Legal|Privacy policy|Modern Slavery Act Transparency Statement|Sitemap|About US| Contact US: help@patsnap.com