Welding process of hydrogenation reaction kettle cylinder body
A hydrogenation reactor and welding process technology, applied in the field of pressure vessels, can solve the problems of different properties of low-alloy steel and stainless steel materials, and easy occurrence of welding cracks, so as to improve the fusion quality and prevent welding cracks
- Summary
- Abstract
- Description
- Claims
- Application Information
AI Technical Summary
Problems solved by technology
Method used
Image
Examples
Embodiment Construction
[0022] From figure 1 It can be seen from the figure that a welding process for hydrogenation reactor cylinder: first, roll the explosively composited plate of 00Cr17Ni14Mo2 stainless steel 1 and 16MnR carbon steel 3 into the required cylinder shape, and sequentially spot-fix at the front end of the required welding position. The arc starting plate and the test plate are fixed at the end of the arc extinguishing plate, and the oil, rust, scale and other harmful impurities within the range of 18-22mm on both sides of the welding groove of the vertical and circular edges to be welded are cleaned; The required welding rods are dried: J507 and HJ350 are dried at 340-360°C and kept for 2 hours, and A042 and A022 are dried at 140-160°C and kept for 1 hour.
[0023] Preheat the required welding parts to not less than 150°C, and perform tack welding. J507 electrode is used for tack welding, welding current is 150-170A, arc voltage is 23-24V, and welding speed is 15-18cm / min; the assemb...
PUM
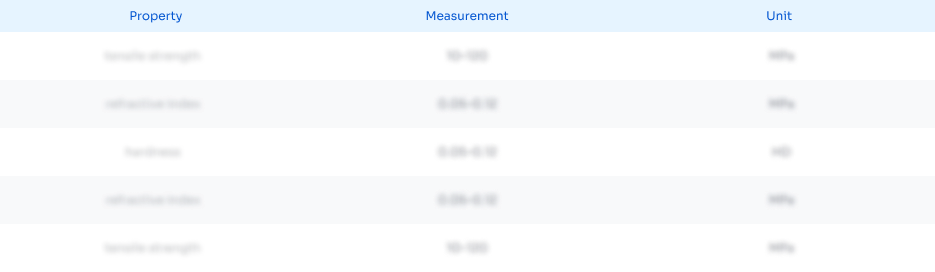
Abstract
Description
Claims
Application Information

- R&D
- Intellectual Property
- Life Sciences
- Materials
- Tech Scout
- Unparalleled Data Quality
- Higher Quality Content
- 60% Fewer Hallucinations
Browse by: Latest US Patents, China's latest patents, Technical Efficacy Thesaurus, Application Domain, Technology Topic, Popular Technical Reports.
© 2025 PatSnap. All rights reserved.Legal|Privacy policy|Modern Slavery Act Transparency Statement|Sitemap|About US| Contact US: help@patsnap.com