Method for winding cardo-containing polyaryletherketone or polyarylethersuifone resin matrix composite
A polyaryletherketone and polyarylethersulfone technology, which is applied in the field of advanced composite material manufacturing, can solve the problems of difficult processing and poor solubility of high-performance thermoplastic resin, and achieve the effects of excellent mechanical properties and low porosity.
- Summary
- Abstract
- Description
- Claims
- Application Information
AI Technical Summary
Problems solved by technology
Method used
Image
Examples
Embodiment 1
[0019] Illustrate the embodiment of the present invention in conjunction with accompanying drawing, under certain tension effect (tension size is controlled by tension device 2), continuous carbon fiber 1 passes through guide roller 3 at a certain speed and impregnates through PEK-C resin solution 4 of certain concentration Glue, so that it is soaked with a certain amount of resin matrix, and then pass through the scraping roller 5 to remove excess glue, and then pass through the drying tunnel 6, and the solvent is removed by drying to obtain a carbon fiber prepreg tape 8, and the solvent is carried out after passing through the exhaust duct 7. Recycling.
[0020] The carbon fiber prepreg tape 8 enters the preheating device 9 for preheating, then utilizes the heat provided by the heating device 10 to melt the matrix resin (the temperature is measured by an infrared thermometer 11), and then winds longitudinally on the surface of the tubular mandrel 12. Under the action of tens...
Embodiment 2
[0023] The present embodiment is described in conjunction with the accompanying drawings. Under a certain tension (the tension is controlled by the tension device 2), the continuous carbon fiber 1 passes through the guide roller 3 at a certain speed and then impregnates it with a certain concentration of PES-C resin solution 4. Soak it with a certain amount of resin matrix, then pass through the scraping roller 5 to remove excess glue, then pass through the drying tunnel 6, and dry to remove the solvent to obtain a carbon fiber prepreg tape 8, and the solvent is recovered after passing through the exhaust duct 7 deal with.
[0024] The carbon fiber prepreg tape 8 enters the preheating device 9 for preheating, then utilizes the heat provided by the heating device 10 to melt the matrix resin (the temperature is measured by an infrared thermometer 11), and then wraps it in a hoop direction on the surface of the annular mandrel 12. Under the action of tension, the pores between th...
Embodiment 3
[0027] In conjunction with the accompanying drawings to illustrate this embodiment, the continuous glass fiber 1 is impregnated with a certain concentration of PEK-C resin solution 4 after passing through the guide roller 3 at a certain speed under a certain tension (the tension is controlled by the tension device 2). , so that it is soaked with a certain amount of resin matrix, and then pass through the scraping roller 5 to remove excess glue, and then pass through the drying tunnel 6, and then dry to remove the solvent to obtain a glass fiber prepreg tape 8, and the solvent passes through the exhaust duct 7 For recycling.
[0028] The glass fiber prepreg tape 8 enters the preheating device 9 for preheating, and then utilizes the heat provided by the heating device 10 to melt the matrix resin (the temperature is measured by an infrared thermometer 11), and then longitudinally and annularly carry out the process on the surface of the tubular mandrel 12. Alternately wrap around...
PUM
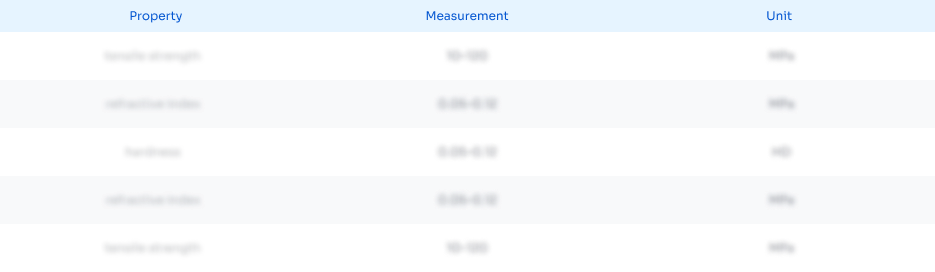
Abstract
Description
Claims
Application Information

- R&D
- Intellectual Property
- Life Sciences
- Materials
- Tech Scout
- Unparalleled Data Quality
- Higher Quality Content
- 60% Fewer Hallucinations
Browse by: Latest US Patents, China's latest patents, Technical Efficacy Thesaurus, Application Domain, Technology Topic, Popular Technical Reports.
© 2025 PatSnap. All rights reserved.Legal|Privacy policy|Modern Slavery Act Transparency Statement|Sitemap|About US| Contact US: help@patsnap.com