Nylon wheel and preparation method thereof
A nylon wheel and nylon fiber technology, applied in chemical instruments and methods, manufacturing tools, and other chemical processes, can solve the problems of blackened workpiece surface, low surface finish, insufficient heat dissipation, etc., and achieve sharp grinding and polishing Good effect, good self-sharpening effect
- Summary
- Abstract
- Description
- Claims
- Application Information
AI Technical Summary
Problems solved by technology
Method used
Image
Examples
Embodiment 1
[0023] The nylon wheel of the present invention includes a nylon fiber screen with a reticular fiber structure and a working layer poured into the nylon fiber screen. The working layer is a mixture made of high-hardness high-quality abrasives, binders, and fillers. The weight ratio of the nylon fiber screen to the above compound is 1:5-7.
[0024] The parts by weight of each component in the above-mentioned mixture are:
[0025] 25-33 parts of high-quality abrasive with high hardness, 40-52 parts of binder, and 9-19 parts of filler.
[0026] Above-mentioned filler comprises magnesium oxide, zinc oxide, chromium oxide, and the relation of the parts by weight of each component in the filler and the parts by weight of each component in the above-mentioned mixture is:
[0027] 1-3 parts of magnesium oxide, 3-6 parts of zinc oxide, and 5-10 parts of chromium oxide.
[0028] Additives are also added to the mixture of the above-mentioned working layer, and the proportion by weight ...
Embodiment 2
[0052] In this embodiment, the weight ratio of the mixture of the working layer before and after the technical solution is changed is specifically:
[0053]
[0054] B. The proportioning by weight of nylon fiber screen and above-mentioned mixture is 1: 7.6;
Embodiment 3
[0056] In this embodiment, the weight ratio of the mixture of the working layer before and after the technical solution is changed is specifically:
[0057]
[0058]
[0059]B. The proportioning by weight of nylon fiber screen and above-mentioned mixture is 1: 7.26;
PUM
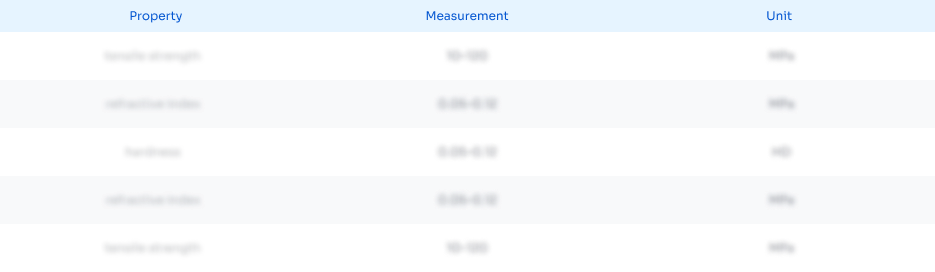
Abstract
Description
Claims
Application Information

- R&D
- Intellectual Property
- Life Sciences
- Materials
- Tech Scout
- Unparalleled Data Quality
- Higher Quality Content
- 60% Fewer Hallucinations
Browse by: Latest US Patents, China's latest patents, Technical Efficacy Thesaurus, Application Domain, Technology Topic, Popular Technical Reports.
© 2025 PatSnap. All rights reserved.Legal|Privacy policy|Modern Slavery Act Transparency Statement|Sitemap|About US| Contact US: help@patsnap.com