Preparation method of microcapsule
A technology of microcapsules and silicon dioxide, applied in the field of microcapsules, can solve problems such as limited controllable range and limited application performance of microcapsules, so as to improve absorption and resistance to external pressure, prevent invagination and dissolution, good controllability
- Summary
- Abstract
- Description
- Claims
- Application Information
AI Technical Summary
Problems solved by technology
Method used
Image
Examples
Embodiment 1
[0036] Add 0.2 g of acryloyloxy to 10.0 g of silica in styrene monomer suspension (the average particle diameter of the silica particles in the suspension is 30 nm, 2.0 g of silica, and 8.0 g of styrene). Propyltrimethoxysilane (MPS), stirred at 70°C for 1 hour in a closed state, added 0.10g of ethylene glycol dimethacrylate and 0.016g of azobisisobutyronitrile, stirred to fully dissolve, and then 1.0 g of dispersant calcium phosphate powder and 49.0 g of deionized water were added thereto to obtain a suspension system. After the above system was sheared and stirred at 300 rpm for 10 minutes under a nitrogen atmosphere, the temperature was raised to 60°C for suspension polymerization for 6 hours, and then heated to 95°C for aging for 1 hour, then cooled and pickled to obtain composite particle powder.
[0037] Soaking the composite particle powder in excess hydrofluoric acid for 24 hours to remove silicon dioxide in the composite particle, and then neutralizing, washing with w...
Embodiment 2
[0040] To 10.0g of silicon dioxide in methyl methacrylate monomer suspension (the average particle diameter of silicon dioxide particles in the suspension is 50nm, silicon dioxide is 1.0g, and methyl methacrylate is 9.0g) 0.2g of acryloyloxypropyltriethoxysilane, stirred at 40°C for 24 hours in a closed state, added 0.045g of ethylene glycol dimethacrylate and 0.18g of dibenzoyl peroxide, stirred to make it After fully dissolving, 0.09 g of dispersant magnesium carbonate powder and 99.0 g of deionized water were added thereto to obtain a suspension system. After the above system was sheared and stirred at 50 rpm for 10 minutes under a nitrogen atmosphere, the temperature was raised to 80°C for suspension polymerization for 2 hours, and then heated to 95°C for aging for 1 hour, then cooled and pickled to obtain composite particle powder.
[0041] Soaking the composite particle powder in excess hydrofluoric acid for 24 hours to remove silicon dioxide in the composite particle, a...
Embodiment 3
[0043] Add 0.2 g of acryloyloxypropane to 10.0 g of silica monomer suspension (the average particle diameter of the silica particles in the suspension is 200 nm, 4.0 g of silica, and 6 g of methyl methacrylate). Trimethoxysilane, stirred at 50°C for 10 hours in a closed state, added 0.24g ethylene glycol dimethacrylate, 0.06g dibenzoyl peroxide and 0.09g azobisisobutyronitrile, and stirred to make It was fully dissolved, and 1.2 g of dispersant calcium phosphate and 99.0 g of deionized water were added thereto to obtain a suspension system. After the above system was sheared and stirred at 100 rpm for 10 minutes under a nitrogen atmosphere, the temperature was raised to 70°C for suspension polymerization for 5 hours, and then heated to 95°C for aging for 1 hour, then cooled and pickled to obtain composite particle powder.
[0044] Soaking the composite particle powder in excess hydrofluoric acid for 24 hours to remove silicon dioxide in the composite particle, and then neutral...
PUM
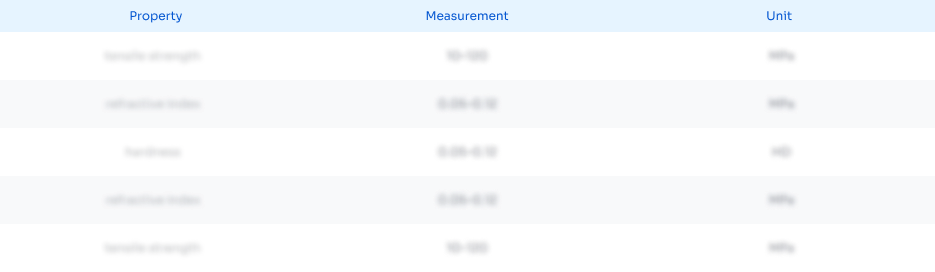
Abstract
Description
Claims
Application Information

- R&D
- Intellectual Property
- Life Sciences
- Materials
- Tech Scout
- Unparalleled Data Quality
- Higher Quality Content
- 60% Fewer Hallucinations
Browse by: Latest US Patents, China's latest patents, Technical Efficacy Thesaurus, Application Domain, Technology Topic, Popular Technical Reports.
© 2025 PatSnap. All rights reserved.Legal|Privacy policy|Modern Slavery Act Transparency Statement|Sitemap|About US| Contact US: help@patsnap.com