Ecological flax yarn and manufacturing process thereof
A manufacturing process, linen yarn technology, applied in the direction of yarn, bleached products, textiles and papermaking, etc., to achieve the effect of high flexibility, good evenness and small hairiness
- Summary
- Abstract
- Description
- Claims
- Application Information
AI Technical Summary
Problems solved by technology
Method used
Examples
Embodiment 1
[0020] Organic hemp is made into hemp sliver, drawn and combined by five or more drawing processes, and then drawn, wound and twisted to make roving. The roving is scoured and bleached, which includes four processes: biological additive L treatment, alkali boiling, oxygen bleaching, and biological additive D treatment:
[0021] Bio-aid L treatment: PH = 7-8, L: 9g / L, JFC: 1g / L, temperature: 55°C, treatment for 75 minutes; alkaline cooking: alkalinity 10g / L, of which NaOH3g / L, NaOH 2 CO 3 19g / L, treat at 95°C for 60 minutes, then wash with water at 85°C for 15 minutes; oxygen bleaching: PH=10.5, add H 2 o 2 : 10.5g / L (30%), Na 2 SiO 3 : 10g / L, JFC: 6g / L, take 30-40 minutes to heat up to 100°C, keep warm for 60 minutes, then wash twice with cold water; treat with an appropriate amount of biological aid D at 40-50°C for 10 minutes. After boiling and bleaching, it is drawn, twisted and spun into a spun yarn, then dried and wound into a bobbin yarn.
Embodiment 2
[0023] Organic hemp is made into hemp sliver, drawn and combined by five or more drawing processes, and then drawn, wound and twisted to make roving. The roving is scoured and bleached, which includes four processes: biological additive L treatment, alkali boiling, oxygen bleaching, and biological additive D treatment:
[0024] Bio-auxiliary L treatment: PH=7-8, L: 8g / L, JFC: 1g / L, temperature: 55°C, treatment for 60-90 minutes; alkaline cooking: alkalinity 10g / L, of which NaOH4g / L, Na 2 CO 3 16g / L, treat at 95°C for 60 minutes, then wash with water at 85°C for 15 minutes; oxygen bleaching: PH=10, add H 2 o 2 : 12g / L (30%), Na 2 SiO 3 : 10g / L, JFC: 6g / L, take 30-40 minutes to heat up to 100°C, keep warm for 60 minutes, then wash twice with cold water; treat with an appropriate amount of biological aid D at 40-50°C for 10 minutes. After boiling and bleaching, it is drawn, twisted and spun into a spun yarn, then dried and wound into a bobbin yarn.
Embodiment 3
[0026] Organic hemp is made into hemp sliver, drawn and combined by five or more drawing processes, and then drawn, wound and twisted to make roving. The roving is scoured and bleached, which includes four processes: biological additive L treatment, alkali boiling, oxygen bleaching, and biological additive D treatment:
[0027] Bio-aid L treatment: PH = 7-8, L: 10g / L, JFC: 1g / L, temperature: 55°C, treatment for 75 minutes; alkaline cooking: alkalinity 10g / L, of which NaOH 5g / L, NaOH 2 CO 3 13g / L, treat at 95°C for 60 minutes, then wash with water at 85°C for 15 minutes; oxygen bleaching: PH=10.5, add H 2 o 2 : 13g / L (30%), Na 2 SiO 3 : 10g / L, JFC: 6g / L, take 30-40 minutes to heat up to 100°C, keep warm for 60 minutes, then wash twice with cold water; treat with an appropriate amount of biological aid D at 40-50°C for 10 minutes. After boiling and bleaching, it is drawn, twisted and spun into a spun yarn, then dried and wound into a bobbin yarn.
PUM
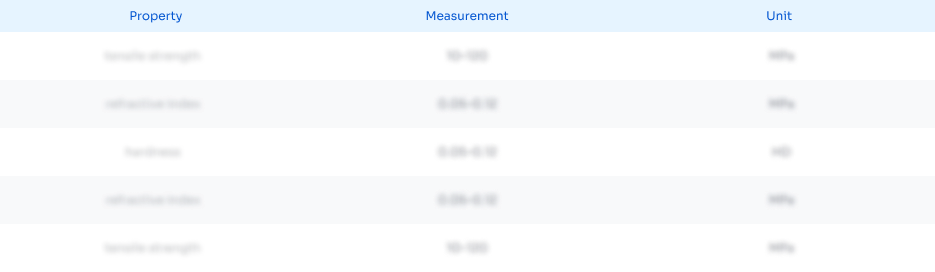
Abstract
Description
Claims
Application Information

- R&D Engineer
- R&D Manager
- IP Professional
- Industry Leading Data Capabilities
- Powerful AI technology
- Patent DNA Extraction
Browse by: Latest US Patents, China's latest patents, Technical Efficacy Thesaurus, Application Domain, Technology Topic, Popular Technical Reports.
© 2024 PatSnap. All rights reserved.Legal|Privacy policy|Modern Slavery Act Transparency Statement|Sitemap|About US| Contact US: help@patsnap.com