Method for extracting TiO 2 and SiO 2 in blast furnace slag
A technology of blast furnace slag and slag powder, which is applied in the direction of silicon dioxide, titanium oxide/hydroxide, titanium dioxide, etc., can solve the problems of high corrosion, large environmental pollution, long process flow, etc., and solve the problems of comprehensive utilization, The effect of large market demand and simple process
- Summary
- Abstract
- Description
- Claims
- Application Information
AI Technical Summary
Problems solved by technology
Method used
Image
Examples
Embodiment 1
[0031] Select a composition (mass percentage) as 21.2% TiO 2 , 22.74% SiO 2 , 26.60% CaO, 8.78% MgO, 12.67% Al 2 o 3 , 5.41% Fe, 0.2% V 2 o 5 The steelmaking blast furnace slag of Panzhihua Iron and Steel Co., Ltd. was used as the reaction raw material. Grinding the blast furnace slag into a powder with a particle size of 325 mesh, weighing 30.0 g of the slag powder after magnetic separation, removing the Fe powder by magnetic separation, adding it to a hydrothermal reaction kettle filled with 24% hydrochloric acid (Tefu dragon liner), stirring constantly. The addition of hydrochloric acid is 1.2 times of theoretical stoichiometric value (stoichiometric is based on CaO, MgO, Al in hydrochloric acid and blast furnace slag 2 o 3 Response prevails). Heat and control the temperature to 150°C, stop heating after 3 hours of reaction. The experimental results show that the dissolution rate of blast furnace slag in the hydrothermal reactor is 52%. The dissolution rate refers...
Embodiment 2
[0034] Select a composition (mass percentage) as 21.2% TiO 2 , 22.74% SiO 2 , 26.60% CaO, 8.78% MgO, 12.67% Al 2 o 3 , 5.41% Fe, 0.2% V 2 o 5 The steelmaking blast furnace slag of Panzhihua Iron and Steel Co., Ltd. was used as the reaction raw material. Grinding the blast furnace slag into a powder with a particle size of 325 mesh, weighing 30.0 g of the slag powder after magnetic separation, removing the Fe powder by magnetic separation, adding it to a hydrothermal reaction kettle filled with 24% hydrochloric acid (Tefu dragon liner), stirring constantly. The addition of hydrochloric acid is 1.2 times of theoretical stoichiometric value (stoichiometric is based on CaO, MgO, Al in hydrochloric acid and blast furnace slag 2 o 3 Response prevails). Heat and control the temperature to 150°C, stop heating after 3 hours of reaction. The experimental results show that the dissolution rate of blast furnace slag in the hydrothermal reactor is 51%. The dissolution rate refers...
Embodiment 3
[0037] Select a composition (mass percentage) as 21.2% TiO 2 , 22.74% SiO 2 , 26.60% CaO, 8.78% MgO, 12.67% Al 2 o 3 , 5.41% Fe, 0.2% V 2 o 5 The steelmaking blast furnace slag of Panzhihua Iron and Steel Co., Ltd. was used as the reaction raw material. Grinding the blast furnace slag into a powder with a particle size of 325 mesh, weighing 30.0 g of the slag powder after magnetic separation, removing the Fe powder by magnetic separation, adding it to a hydrothermal reaction kettle filled with 22% hydrochloric acid (Tefu dragon liner), stirring constantly. The addition of hydrochloric acid is 1.2 times of theoretical stoichiometric value (stoichiometric is based on CaO, MgO, Al in hydrochloric acid and blast furnace slag 2 o 3 Response prevails). Heat and control the temperature to 150°C, stop heating after 3 hours of reaction. The experimental results show that the dissolution rate of blast furnace slag in the hydrothermal reactor is 51%. The dissolution rate refers...
PUM
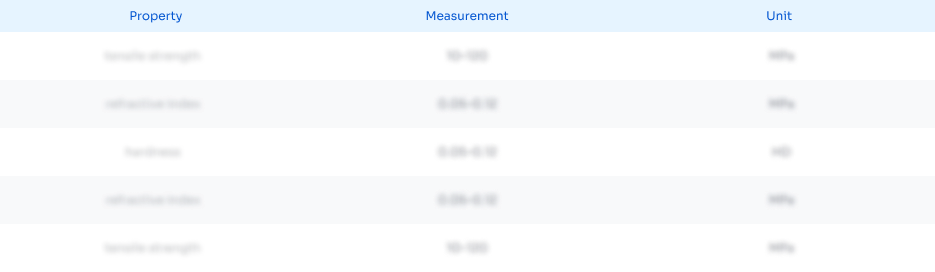
Abstract
Description
Claims
Application Information

- Generate Ideas
- Intellectual Property
- Life Sciences
- Materials
- Tech Scout
- Unparalleled Data Quality
- Higher Quality Content
- 60% Fewer Hallucinations
Browse by: Latest US Patents, China's latest patents, Technical Efficacy Thesaurus, Application Domain, Technology Topic, Popular Technical Reports.
© 2025 PatSnap. All rights reserved.Legal|Privacy policy|Modern Slavery Act Transparency Statement|Sitemap|About US| Contact US: help@patsnap.com