Cutting method of crystalline silicon blocks
A cutting method and technology for silicon blocks, which are used in grinding machines, fine working devices, metal processing equipment, etc., can solve the problem of small silicon fragments falling into the wire saw mesh or guide wheel, reducing the service life of the guide wheel, wire breakage, etc. Jumper and other problems, to achieve the effect of improving the yield of slicing, the quality of silicon wafers, and improving the stability
- Summary
- Abstract
- Description
- Claims
- Application Information
AI Technical Summary
Problems solved by technology
Method used
Image
Examples
Embodiment 1
[0027] In this technical scheme, the 264 model slicer of Swiss MB company is used to cut the crystalline silicon block into slices.
[0028] like figure 1 , figure 2 , image 3 , Figure 4 As shown in the figure, several short silicon blocks 21 of different lengths are sent to the end face grinding CNC machine tool to be ground flat, so that the originally uneven end face 23 is flattened into an end face 24 with an inclination of not more than 200 microns, and then the short silicon blocks with the flat end face are flattened. 21 is glued to the base glass 30, there is a splicing seam 22 in between, and its total effective length is 760mm, and the base glass crystal 30 with the short silicon block 21 glued is installed on the working table 10 of the slicing machine to become a cutting workpiece.
[0029] When slicing is started, the workpiece is slowly pressed down, and the pre-prepared mortar is supplied to the wire saw 50 by the motor. The guide wheel 40 drives the wire ...
Embodiment 2
[0031] like figure 1 , figure 2 , image 3 , Figure 4 As shown, in this technical solution, the 264 model slicer of Swiss MB company is used to cut the crystalline silicon block into slices.
[0032] Several short silicon blocks 21 are directly arranged and glued to the base glass 30, and the crystalline silicon blocks with a total effective length of 760 mm are directly mounted on the worktable 10 of the slicer to become a cutting workpiece.
[0033] When slicing is started, the workpiece is slowly pressed down, and the pre-prepared mortar is supplied to the wire saw 50 by the motor. The guide wheel 40 drives the wire saw to rotate. The silicon block is rubbed at high speed to achieve the purpose of cutting, and the whole slicing process takes 7.5 hours.
Embodiment 3
[0035] like figure 1 , figure 2 , image 3 , Figure 4 As shown, in this technical solution, the crystalline silicon block is cut into slices by using the B5 slicer of HCT Company in Switzerland.
[0036] like figure 1 , figure 2 , image 3 As shown in the figure, several short silicon blocks 21 of different lengths are sent to the end face grinding CNC machine tool to be ground flat, so that the originally uneven end face 23 is flattened into an end face 24 with an inclination of not more than 200 microns, and then the short silicon blocks with the flat end face are flattened. 21 is glued to the base glass 30, leaving a splicing seam 22 in between, and its total effective length is 860 mm. After the base glass crystal 30 glued with the short silicon block 21 is installed on the worktable 10 of the slicer, it becomes a cutting workpiece .
[0037] When slicing is started, the workpiece is slowly pressed down, and the pre-prepared mortar is supplied to the wire saw 50 ...
PUM
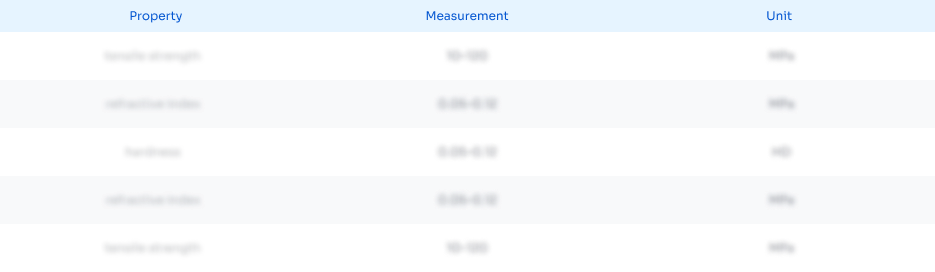
Abstract
Description
Claims
Application Information

- R&D
- Intellectual Property
- Life Sciences
- Materials
- Tech Scout
- Unparalleled Data Quality
- Higher Quality Content
- 60% Fewer Hallucinations
Browse by: Latest US Patents, China's latest patents, Technical Efficacy Thesaurus, Application Domain, Technology Topic, Popular Technical Reports.
© 2025 PatSnap. All rights reserved.Legal|Privacy policy|Modern Slavery Act Transparency Statement|Sitemap|About US| Contact US: help@patsnap.com