Technique process of grainy calcium material for preventing and treating peanut blight
A material, peanut technology, applied in the field of granular calcium material production process, can solve the problems of high local concentration, easy loss of shell powder, burn skin, etc., to achieve the effect of saving resources, large application and promotion value, and increasing production
- Summary
- Abstract
- Description
- Claims
- Application Information
AI Technical Summary
Problems solved by technology
Method used
Examples
Embodiment 1
[0016] Weigh 85 kg of shell powder of 80 mesh and 15 kg of weathered coal of 80 mesh, and fully mix them evenly.
[0017] First, transport 50kg of the mixed material to the disc granulator for granulation. The speed of the granulator is controlled at 30-45r / min, and water is sprayed intermittently. The remaining material makes the core grow gradually, and finally reaches the desired particle (between 1.0-3.5mm); the control time of the granulation process is 15-25min. The granulated granular materials are directly dried in the sun or transported to a dryer at 80-100°C for drying, so that the moisture content is not higher than 2.5%. Then the dried material is sieved through a sieve, and finally the particle size of the finished product is controlled between 1.0-3.5mm, and the finished product rate can generally reach 80-85%. Unqualified products are crushed by a pulverizer and then re-granulated.
Embodiment 2
[0019] Weigh 80kg of 80-mesh shell powder and 20kg of 80-mesh weathered coal, and fully mix the two evenly.
[0020] First, transport 40kg of the mixed material to the disc granulator for granulation. The speed of the granulator is controlled at 30-45r / min, and water is sprayed intermittently. The remaining material makes the core grow gradually, and finally reaches the desired particle (between 1.0-3.5mm). The control time of the granulation process is 15-25min. The granulated granular materials are directly dried in the sun or transported to a dryer at 80-100°C for drying, so that the moisture content is not higher than 2.5%. Then the dried material is sieved through a sieve, and finally the particle size of the finished product is controlled between 1.0-3.5mm, and the finished product rate can generally reach 80-85%. Unqualified products are crushed by a pulverizer and then re-granulated.
Embodiment 3
[0022] Weigh 82 kg of shell powder of 80 mesh and 18 kg of weathered coal of 80 mesh, and fully mix them evenly.
[0023] First, transport 60kg of the mixed material to the disc granulator for granulation. The speed of the granulator is controlled at 30-45r / min, and water is sprayed intermittently. The remaining material makes the core grow gradually, and finally reaches the desired particle (between 1.0-3.5mm). The control time of the granulation process is 15-25min. The granulated granular materials are directly dried in the sun or transported to a dryer at 80-100°C for drying, so that the moisture content is not higher than 2.5%. Then the dried material is sieved through a sieve, and finally the particle size of the finished product is controlled between 1.0-3.5mm, and the finished product rate can generally reach 80-85%. Unqualified products are crushed by a pulverizer and then re-granulated.
[0024] The invention is full of novelty and reasonable in design, not only h...
PUM
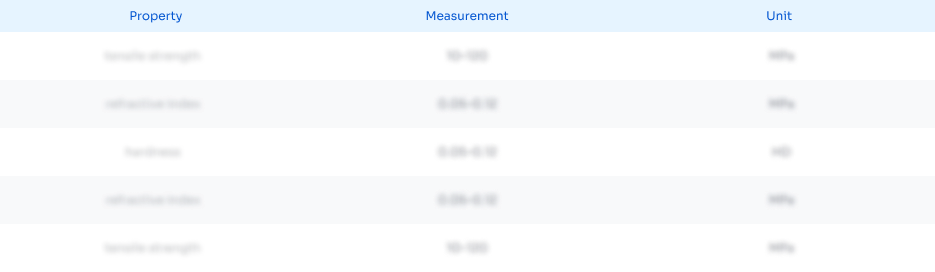
Abstract
Description
Claims
Application Information

- Generate Ideas
- Intellectual Property
- Life Sciences
- Materials
- Tech Scout
- Unparalleled Data Quality
- Higher Quality Content
- 60% Fewer Hallucinations
Browse by: Latest US Patents, China's latest patents, Technical Efficacy Thesaurus, Application Domain, Technology Topic, Popular Technical Reports.
© 2025 PatSnap. All rights reserved.Legal|Privacy policy|Modern Slavery Act Transparency Statement|Sitemap|About US| Contact US: help@patsnap.com