A heat treatment method that improves the formability and bake hardenability of 6XXX series aluminum alloy sheets
A heat treatment method and bake hardening technology, which is applied in the field of preheating, can solve the problems of limited ability to strengthen plate paint, limit the application of 6016 aluminum alloy, and short time of bake hardening performance, so as to achieve the retention time of bake hardening performance The effect of prolonging, saving energy and equipment investment, improving machining accuracy and surface quality
- Summary
- Abstract
- Description
- Claims
- Application Information
AI Technical Summary
Problems solved by technology
Method used
Image
Examples
Embodiment 1
[0028] After the aluminum alloy ingot is homogenized in a circulating air resistance furnace at 470°C×5h+540°C×15h, it is cut and face milled, hot rolled, intermittently annealed and finally cold rolled into a thin plate with a thickness of 1mm. After the sheet was quenched by solution treatment at 560°C×30min in an air circulation resistance furnace, it was immediately treated in an oil bath furnace at 65°C×5h, and then parked at room temperature for 1 month, 2 months, 3 months and Hardness test and tensile test were carried out after 4 months. The simulated paint baking is carried out in an oil bath furnace at a temperature of 180°C×30min. After the paint is baked, the hardness test and tensile test are carried out.
Embodiment 2
[0030] After the aluminum alloy ingot is homogenized in a circulating air resistance furnace at 470°C×5h+540°C×15h, it is cut and face milled, hot rolled, intermittently annealed and finally cold rolled into a thin plate with a thickness of 1mm. After the thin plate was quenched by solution treatment at 560°C×30min in an air circulation resistance furnace, it was immediately treated in an oil bath furnace at 65°C×15h, and then parked at room temperature for 1 month, 2 months, 3 months and Hardness test and tensile test were carried out after 4 months. The simulated paint baking is carried out in an oil bath furnace at a temperature of 180°C×30min. After the paint is baked, the hardness test and tensile test are carried out.
Embodiment 3
[0032] After the aluminum alloy ingot is homogenized in a circulating air resistance furnace at 470°C×5h+540°C×15h, it is cut and face milled, hot rolled, intermittently annealed and finally cold rolled into a thin plate with a thickness of 1mm. After the sheet was quenched by solution treatment at 560°C×30min in an air circulation resistance furnace, it was immediately treated in an oil bath furnace at 65°C×25h, and then parked at room temperature for 1 month, 2 months, 3 months and Hardness test and tensile test were carried out after 4 months. The simulated paint baking is carried out in an oil bath furnace at a temperature of 180°C×30min. After the paint is baked, the hardness test and tensile test are carried out.
PUM
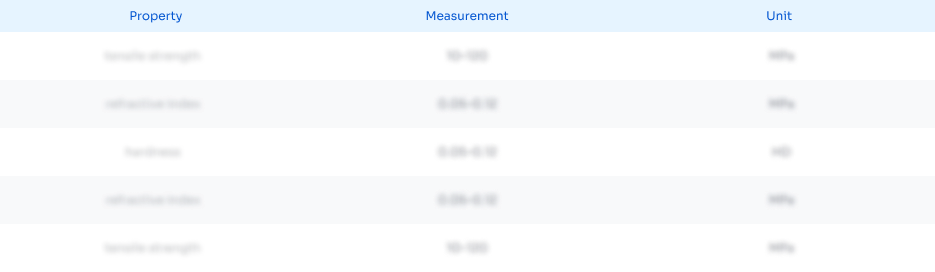
Abstract
Description
Claims
Application Information

- R&D
- Intellectual Property
- Life Sciences
- Materials
- Tech Scout
- Unparalleled Data Quality
- Higher Quality Content
- 60% Fewer Hallucinations
Browse by: Latest US Patents, China's latest patents, Technical Efficacy Thesaurus, Application Domain, Technology Topic, Popular Technical Reports.
© 2025 PatSnap. All rights reserved.Legal|Privacy policy|Modern Slavery Act Transparency Statement|Sitemap|About US| Contact US: help@patsnap.com