Method for synchronizing anode polyacrylamide latex
A technology of polyacrylamide and synthesis method, which is applied in the field of synthesis of cationic polyacrylamide emulsion, and can solve the problems of low effective content, limited use effect, low molecular weight, etc.
- Summary
- Abstract
- Description
- Claims
- Application Information
AI Technical Summary
Problems solved by technology
Method used
Examples
Embodiment 1
[0018] Embodiment 1, component and weight ratio:
[0019] Acrylamide 134
[0020] Methacryloyloxyethyltriammonium Chloride 40
[0021] Deionized water 249
[0022] Span-80 2.3
[0023] Ammonium persulfate / sodium bisulfite 0.65
[0024] Sodium bisulfite 0.68
[0025] Toluene 55
[0026] Nonylphenol polyoxyethylene ether 10-20
[0027] Processing conditions:
[0028] 1. Dissolve and mix acrylamide, methacryloyloxyethyltrimethylammonium chloride and deionized water evenly to obtain a water phase.
[0029] 2. Dissolve Span-80 in part of toluene to obtain the oil phase, add the water phase, oil phase, remaining toluene and ammonium persulfate / sodium bisulfite into the reaction kettle, and stir evenly.
[0030] 3. Under nitrogen protection, raise the temperature to 25°C and react at 25°C for 3 hours.
[0031] 4. After the reaction time is up, add sodium bisulfite to remove residual monomers, filter, and add a phase inversion agent (nonylphenol polyoxyethylene ether) at room...
Embodiment 2
[0032] Embodiment 2, component and weight ratio:
[0033] N.N-dimethylacrylamide 52
[0034] Acrylamidopropyl dimethyl benzyl ammonium chloride 345
[0035] Deionized water 398
[0036] Span-80 2.3
[0037] Potassium sulfate / sodium bisulfite 0.80
[0038] Sodium bisulfite 0.68
[0039] Xylene 55
[0040] Nonylphenol polyoxyethylene ether 10-20
[0041] Processing conditions:
[0042] 1. Dissolve and mix N.N-dimethylacrylamide, acrylamidopropyl dimethyl benzyl ammonium chloride and deionized water evenly to obtain a water phase.
[0043] 2 Dissolve Span-80 in part of xylene to obtain an oil phase, add the water phase, oil phase, remaining xylene and potassium sulfate / sodium bisulfite into the reaction kettle, and stir evenly.
[0044] 3. Under nitrogen protection, raise the temperature to 30°C and react for 3 hours.
[0045] 4. After the reaction time is up, add sodium bisulfite to remove residual monomers, filter, and add a phase inversion agent (nonylphenol polyoxyet...
Embodiment 3
[0047] Components and weight ratio:
[0048] N-methacrylamide 268
[0049] Acryloyloxyethyltrimethylammonium chloride 61
[0050] Deionized water 116
[0051] Span-80 2.3
[0052] Initiator V044 0.35
[0053] Sodium bisulfite 0.68
[0054] Benzene 55
[0055] Nonylphenol polyoxyethylene ether 10-20
[0056] 1. Dissolve and mix N-methacrylamide, acryloyloxyethyltrimethylammonium chloride and deionized water evenly to obtain a water phase.
[0057] 2 Dissolve Span-80 in part of benzene to obtain the oil phase, add the water phase, oil phase, remaining benzene and initiator into the reaction kettle and stir evenly.
[0058] 3. Under nitrogen protection, raise the temperature to 40°C and react for 3 hours.
[0059]4. After the reaction time is up, add sodium bisulfite to remove residual monomers, filter, and add a phase inversion agent (nonylphenol polyoxyethylene ether) at room temperature to adjust the properties of the latex to obtain the product.
PUM
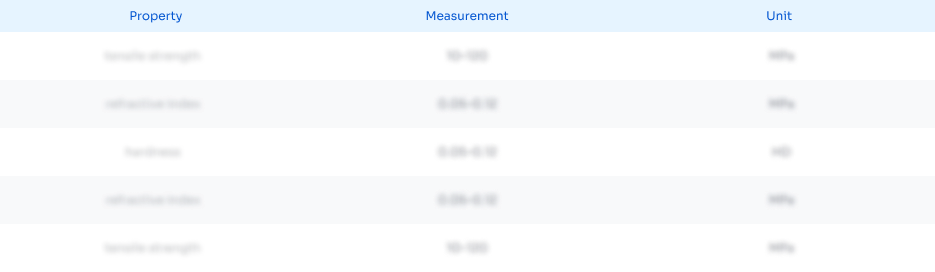
Abstract
Description
Claims
Application Information

- Generate Ideas
- Intellectual Property
- Life Sciences
- Materials
- Tech Scout
- Unparalleled Data Quality
- Higher Quality Content
- 60% Fewer Hallucinations
Browse by: Latest US Patents, China's latest patents, Technical Efficacy Thesaurus, Application Domain, Technology Topic, Popular Technical Reports.
© 2025 PatSnap. All rights reserved.Legal|Privacy policy|Modern Slavery Act Transparency Statement|Sitemap|About US| Contact US: help@patsnap.com