Three-degree-of-freedom-motion permanent magnetic spherical step motor
A stepping motor, degree of freedom technology, applied in the direction of electric components, magnetic circuit shape/style/structure, electrical components, etc., can solve the problems affecting the dynamic response and positioning accuracy of the rotor, increase friction resistance, etc., to improve the dynamic response and Positioning accuracy, avoiding frictional resistance, reducing the effect of the moment of inertia
- Summary
- Abstract
- Description
- Claims
- Application Information
AI Technical Summary
Problems solved by technology
Method used
Image
Examples
Embodiment Construction
[0035] see figure 1 , figure 2 , in order to reduce the moment of inertia, in the spherical rotor, the upper hemispherical shell and the lower hemispherical shell made of non-magnetic materials are interlocked to form a hollow rotor spherical shell 1, and the tightening bolt 10 and positioning pin 16 fixed on the output shaft 6 Stitch the upper and lower hemispherical shells together.
[0036] On the hollow rotor spherical shell 1, four layers of permanent magnet slots 12 are distributed at intervals of equal longitude and equal latitude, and the cylindrical permanent magnets 14 arranged in the radial direction of the hollow rotor spherical shell 1 in the adjacent permanent magnet slots 12 are N The poles and S poles are alternately distributed; the height-adjustable bottom annular ball bearing 8 fixed on the base 7 is supported on the bottom of the hollow rotor spherical shell 1, and the bottom annular ball bearing 8 is made of non-magnetic material. The spherical rotor and...
PUM
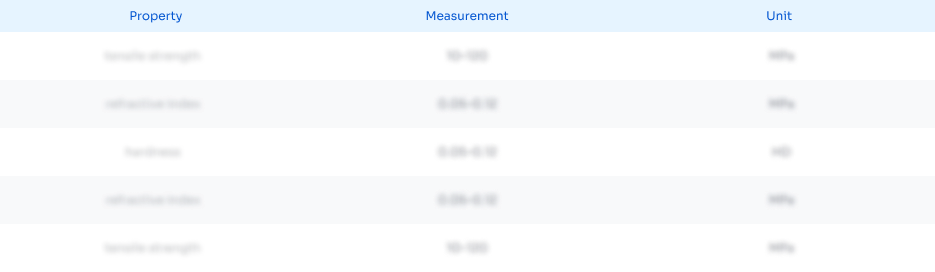
Abstract
Description
Claims
Application Information

- R&D
- Intellectual Property
- Life Sciences
- Materials
- Tech Scout
- Unparalleled Data Quality
- Higher Quality Content
- 60% Fewer Hallucinations
Browse by: Latest US Patents, China's latest patents, Technical Efficacy Thesaurus, Application Domain, Technology Topic, Popular Technical Reports.
© 2025 PatSnap. All rights reserved.Legal|Privacy policy|Modern Slavery Act Transparency Statement|Sitemap|About US| Contact US: help@patsnap.com