Thermoplastic polyurethane floor tile and technique for producing the same
A technology of thermoplastic polyurethane and floor tiles, which is applied in the direction of architecture, building structure, floor, etc., can solve problems such as easy to break, easy to pollute the environment, and harmful effects on the nervous system, and achieve high safety in use, high surface hardness, and pattern rich effect
- Summary
- Abstract
- Description
- Claims
- Application Information
AI Technical Summary
Problems solved by technology
Method used
Image
Examples
Embodiment 1
[0053] Example 1: Processing of new TPU raw materials
[0054] Midsole material layer: TPU: CaCO 3 =20-30kg: 70-80kg.
[0055] Primer layer: TPU: CaCO 3 =32.5-42.5kg: 56.5-66.5kg.
[0056] refer to figure 1 and figure 2 , the wear-resistant layer 1, the printing layer 2 and the base layer 3 are respectively processed and cut into slices according to the production specifications, and passed the inspection, and several sheets are neatly stacked on the pallet for use. Among them, the wear-resistant layer 1 is a sheet made of TPU raw material through extrusion and casting equipment. According to the design requirements, a wear-resistant layer material with a thickness of 0.1-2.0mm can be processed; the printing layer 2 is TPU raw material through blow molding or stretching equipment. , process a printing layer film with a thickness of 0.05-1.0mm, and then print a color pattern through offset printing; the base layer 3 is divided into two layers, namely the middle bottom mat...
Embodiment 2
[0060] Example 2 TPU new material and recycled material processing
[0061] The basic process is the same as the above example, wherein the raw materials of the base layer are mixed in parts by weight: 50 parts of TPU new material + 50 parts of TPU recycled material to form 100 parts of TPU mixture, and the mixture is divided into two parts on average. The formula is:
[0062] Midsole material layer: 50 parts of TPU mixture + 122-132 parts of stone powder (CaCO 3 )
[0063] Bottom material layer: 50 parts of TPU mixture + 62-72 parts of stone powder (CaCO 3 )
[0064] The raw materials are mixed, mixed by high-speed mixing and mixing equipment, and pressed into small pieces that can be glued. Pressurization parameters: pressurize for 2 minutes for the first time, stop for 0.8 minutes in the middle, turn the material, and pressurize for 1 minute for the second time; thermal compound parameters: preheating temperature between 120-135°C, hot pressing after preheating, the pres...
Embodiment 3
[0065] Embodiment Three Processing of all TPU recycled materials
[0066] The basic process is the same as the above example, wherein the TPU raw materials in the base layer are all recycled materials, and the formula is as follows according to the parts by weight:
[0067] Midsole material layer: 50 parts of TPU recycled material + 105-110 parts of stone powder (CaCO 3 )
[0068] Bottom material layer: 50 parts of TPU recycled material + 56-61 parts of stone powder (CaCO 3 )
[0069] The raw materials are mixed, mixed by high-speed mixing and mixing equipment, and pressed into small pieces that can be glued. Pressurization parameters: pressurize for 2 minutes for the first time, stop for 0.8 minutes in the middle, turn the material, and pressurize for 1 minute for the second time; thermal compound parameters: preheating temperature between 120-135°C, hot pressing after preheating, the pressure is at Control at 0.60-0.80mpa, saturation temperature 135-140°C, heat press for...
PUM
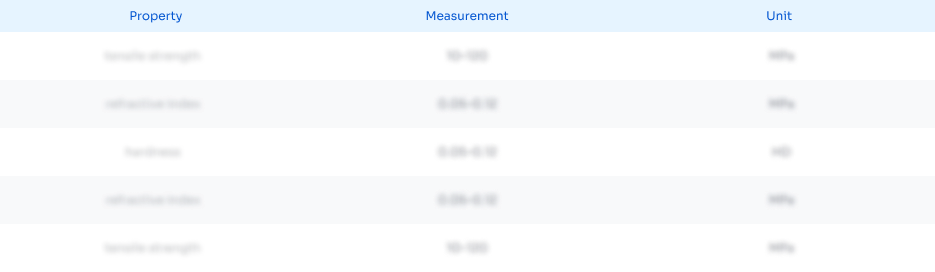
Abstract
Description
Claims
Application Information

- R&D
- Intellectual Property
- Life Sciences
- Materials
- Tech Scout
- Unparalleled Data Quality
- Higher Quality Content
- 60% Fewer Hallucinations
Browse by: Latest US Patents, China's latest patents, Technical Efficacy Thesaurus, Application Domain, Technology Topic, Popular Technical Reports.
© 2025 PatSnap. All rights reserved.Legal|Privacy policy|Modern Slavery Act Transparency Statement|Sitemap|About US| Contact US: help@patsnap.com