Process for direct reduction of liquid high-lead skim with reduction furnace
A reduction furnace and high lead slag technology, applied in the field of lead smelting, can solve the problems of difficult recovery of sulfur dioxide flue gas, unorganized emission and lead dust pollution cannot be effectively controlled, and achieve improved labor productivity, large production capacity, coke The effect of reducing consumption and flue gas volume
- Summary
- Abstract
- Description
- Claims
- Application Information
AI Technical Summary
Problems solved by technology
Method used
Image
Examples
Embodiment Construction
[0014] Referring to the accompanying drawings, a reduction furnace directly reduces liquid high-lead slag technology, using secondary lead-containing materials such as liquid high-lead slag, lead concentrate, waste miscellaneous lead, waste batteries, etc. The raw materials are added from the top of the reduction furnace, and the pulverized coal and natural gas as fuel and the oxygen-enriched air as a combustion accelerant are passed through the top of the reduction furnace continuously, and then the combustion reaction occurs, and the temperature in the reduction furnace is kept at 1000-1500 ° C; pulverized coal Natural gas is used as a reducing agent at the same time, and it is fully mixed with the raw material and then falls into the reaction pool at the bottom of the reduction furnace to reduce the lead oxide in the raw material to crude lead. The amount of reducing agent added is to fully reduce the lead oxide in the raw material The lead oxide shall prevail, and the zinc ...
PUM
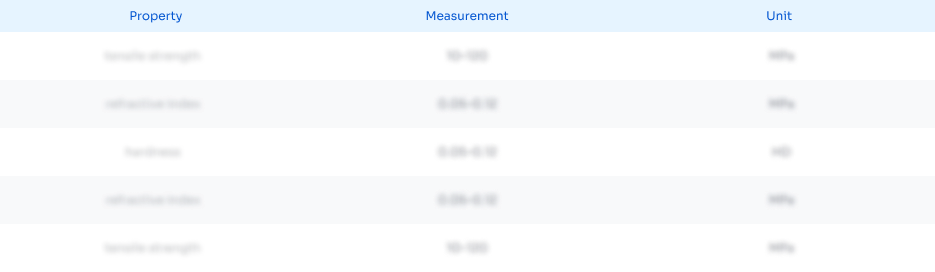
Abstract
Description
Claims
Application Information

- R&D
- Intellectual Property
- Life Sciences
- Materials
- Tech Scout
- Unparalleled Data Quality
- Higher Quality Content
- 60% Fewer Hallucinations
Browse by: Latest US Patents, China's latest patents, Technical Efficacy Thesaurus, Application Domain, Technology Topic, Popular Technical Reports.
© 2025 PatSnap. All rights reserved.Legal|Privacy policy|Modern Slavery Act Transparency Statement|Sitemap|About US| Contact US: help@patsnap.com