Manufacturing method of semiconductor device
A manufacturing method, semiconductor technology, applied in semiconductor/solid-state device manufacturing, semiconductor devices, semiconductor/solid-state device components, etc., can solve the problem of inability to form aluminum sidewall protection film, difficulty in forming large pseudo-patterns, and inability to supply corrosion resistance Agent decomposition and other issues
- Summary
- Abstract
- Description
- Claims
- Application Information
AI Technical Summary
Problems solved by technology
Method used
Image
Examples
Embodiment Construction
[0014] Hereinafter, an embodiment of the present invention will be described based on FIGS. 1 and 2.
[0015] Fig. 1 is a process sectional view showing a first embodiment of the present invention.
[0016] 1(A) shows a process in the middle of forming a semiconductor element on a semiconductor substrate 102, and is a cross-sectional view showing a process of forming a trench 100 after forming a contact hole of the semiconductor element. An interlayer insulating film 103 is formed on the semiconductor substrate 102, and a resist 101 is coated on the interlayer insulating film. The resist 101 is patterned, and using it as a mask, trenches 100 in the form of openings are formed in the underlying interlayer insulating film 103 and the semiconductor substrate 102 by etching. When the semiconductor element does not have a trench structure, a mask is added after forming the contact hole to form the trench 100 as in this embodiment. However, if it is a semiconductor element with a trench...
PUM
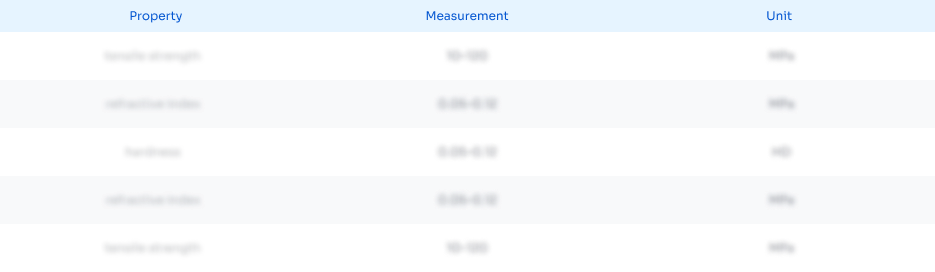
Abstract
Description
Claims
Application Information

- R&D Engineer
- R&D Manager
- IP Professional
- Industry Leading Data Capabilities
- Powerful AI technology
- Patent DNA Extraction
Browse by: Latest US Patents, China's latest patents, Technical Efficacy Thesaurus, Application Domain, Technology Topic, Popular Technical Reports.
© 2024 PatSnap. All rights reserved.Legal|Privacy policy|Modern Slavery Act Transparency Statement|Sitemap|About US| Contact US: help@patsnap.com