Method for preparing Bi2Te3 / carbon nano-tube composite material
A carbon nanotube and composite material technology, applied in the fields of nanostructure manufacturing, nanotechnology, nanotechnology, etc., can solve the problems of long time required, complex chemical reaction, difficult control of the reaction system, etc., to improve thermoelectric performance and simple process. Effect
- Summary
- Abstract
- Description
- Claims
- Application Information
AI Technical Summary
Problems solved by technology
Method used
Image
Examples
Embodiment 1
[0018] 1) Weigh a certain amount of Na 2 TeO 3 and Bi(NO 3 ) 3 ·5H 2 O, respectively dissolved in ethylene glycol to make 0.1875mmmol / l and 0.5mmol / l ethylene glycol solutions, according to Bi 2 Te 3 The mol ratio of Bi:Te determined by the chemical composition is 2:3, and 16.0ml Na 2 TeO 3 ethylene glycol solution and 4.0ml Bi(NO 3 ) 3 ·5H 2 O and ethylene glycol solution were mixed, mixed evenly and then transferred to the burette of the microwave reactor.
[0019] 2) Ultrasonic dispersion of 0.16 g of treated carbon nanotubes in ethylene glycol was transferred to a 100 ml three-neck round bottom flask, and the pH was adjusted to 13. The treatment method of carbon nanotubes is: put carbon nanotubes in concentrated nitric acid and heat them to 120°C, oxidize them for 3 hours, wash them with deionized water until neutral, remove impurities, and then ultrasonically disperse carbon nanotubes in concentrated ammonia water for 2 hours , and washed again to neutrality, p...
Embodiment 2
[0023] 1) Weigh a certain amount of TeO 2 and Bi(NO 3 ) 3 ·5H 2 O, respectively dissolved in ethylene glycol to make 0.1875mmmol / l and 0.5mmol / l ethylene glycol solutions, according to Bi 2 Te 3 The molar ratio of Bi:Te determined by the chemical composition is 2:3, and 16.0ml TeO 2 ethylene glycol solution and 4.0ml Bi(NO 3 ) 3 ·5H 2 O and ethylene glycol solution were mixed, mixed evenly and then transferred to the burette of the microwave reactor.
[0024] 2) Ultrasonic dispersion of 0.08 g of the treated carbon nanotubes in ethylene glycol was transferred to a 100 ml three-necked round bottom flask, and the pH was adjusted to 11. The treatment method of carbon nanotubes is: put carbon nanotubes in concentrated nitric acid and heat them to 120°C, oxidize them for 3 hours, wash them with deionized water until neutral, remove impurities, and then ultrasonically disperse carbon nanotubes in concentrated ammonia water for 2 hours , and washed again to neutrality, place...
Embodiment 3
[0028] 1) Weigh a certain amount of Te and BiCl 3 , respectively dissolved in ethylene glycol to make 0.1875mmmol / l and 0.5mmol / l ethylene glycol solutions, according to Bi 2 Te 3 The molar ratio of Bi:Te determined by the chemical composition is 2:3, the ethylene glycol solution of 16.0ml Te and 4.0ml BiCl 3 The ethylene glycol solution was mixed, mixed evenly and then transferred to the burette of the microwave reactor.
[0029]2) Ultrasonic dispersion of 1.6 g of treated carbon nanotubes in ethylene glycol was transferred to a 100 ml three-necked round bottom flask, and the pH was adjusted to 14. The treatment method of carbon nanotubes is: put carbon nanotubes in concentrated nitric acid and heat them to 120°C, oxidize them for 3 hours, wash them with deionized water until neutral, remove impurities, and then ultrasonically disperse carbon nanotubes in concentrated ammonia water for 2 hours , and washed again to neutrality, placed in a concentrated solution of EDTA and ...
PUM
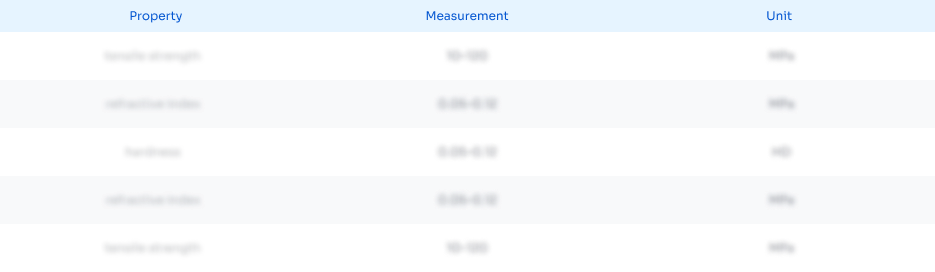
Abstract
Description
Claims
Application Information

- Generate Ideas
- Intellectual Property
- Life Sciences
- Materials
- Tech Scout
- Unparalleled Data Quality
- Higher Quality Content
- 60% Fewer Hallucinations
Browse by: Latest US Patents, China's latest patents, Technical Efficacy Thesaurus, Application Domain, Technology Topic, Popular Technical Reports.
© 2025 PatSnap. All rights reserved.Legal|Privacy policy|Modern Slavery Act Transparency Statement|Sitemap|About US| Contact US: help@patsnap.com