High-carbon steel wire for superfine steel wire and manufacturing method thereof
A manufacturing method and technology for high carbon steel, applied in the direction of manufacturing tools, temperature control, process efficiency improvement, etc., can solve problems such as broken wires, improve production efficiency and yield, excellent cold working performance, and simplify the drawing process. Effect
- Summary
- Abstract
- Description
- Claims
- Application Information
AI Technical Summary
Problems solved by technology
Method used
Image
Examples
Embodiment 1
[0039] A high-carbon steel wire rod for ultra-fine steel wire, the chemical composition of which is C: 0.61, Si: 0.48, Mn: 0.60, P: 0.020, S: 0.019, Ti: 0.0020, Al: 0.005, N: 0.0059 , the balance is Fe and unavoidable inclusions.
[0040] The manufacturing method of the high-carbon steel wire includes the following steps: 1) smelting according to the ultra-pure steel process, 2) desulfurization of molten iron, 3) compound blowing at the top and bottom of the converter, 4) refining with argon blowing in the ladle, 5) refining outside the furnace, 6) Casting into a billet, 7) Austenitizing treatment in a heating furnace, 8) Controlled rolling and controlled cooling treatment of high-speed wire rods to finally obtain wire rods. Wherein: in step 4) and step 5), molten steel refining adopts CaO / SiO 2 =1.6 low-alkalinity steel slag; in step 5), the argon flow rate of the molten steel blown and stirred by argon is 45l / min, and the stirring time is 45min; in step 7), the temperature ...
Embodiment 2
[0043] A high-carbon steel wire rod for ultra-fine steel wire, the chemical composition of which is C: 0.70, Si: 0.20, Mn: 0.60, P: 0.020, S: 0.015, Ti: 0.0015, Al: 0.005, N: 0.0058 by weight percentage , the balance is Fe and unavoidable inclusions.
[0044] The manufacturing method of the high-carbon steel wire includes the following steps: 1) smelting according to the ultra-pure steel process, 2) desulfurization of molten iron, 3) compound blowing at the top and bottom of the converter, 4) refining with argon blowing in the ladle, 5) refining outside the furnace, 6) Casting into a billet, 7) Austenitizing treatment in a heating furnace, 8) Controlled rolling and controlled cooling treatment of high-speed wire rods to finally obtain wire rods. Wherein: in step 4) and step 5), molten steel refining adopts CaO / SiO 2 =0.5 low-alkalinity steel slag; in step 5), the argon flow rate of molten steel blown and stirred by argon is 35l / min, and the stirring time is 60min; in step 7),...
Embodiment 3
[0047] A high-carbon steel wire rod for ultra-fine steel wire, the chemical composition of which is C: 0.85, Si: 0.15, Mn: 0.40, P: 0.015, S: 0.007, Ti: 0.0011, Al: 0.004, N: 0.0050 , the balance is Fe and unavoidable inclusions.
[0048] The manufacturing method of the high-carbon steel wire includes the following steps: 1) smelting according to the ultra-pure steel process, 2) desulfurization of molten iron, 3) compound blowing at the top and bottom of the converter, 4) refining with argon blowing in the ladle, 5) refining outside the furnace, 6) Casting into a billet, 7) Austenitizing treatment in a heating furnace, 8) Controlled rolling and controlled cooling treatment of high-speed wire rods to finally obtain wire rods. Wherein: in step 4) and step 5), molten steel refining adopts CaO / SiO 2 =1.5 low-alkalinity steel slag; in step 5), the argon flow rate of molten steel blown and stirred by argon is 300l / min, and the stirring time is 30min; in step 7), the temperature of ...
PUM
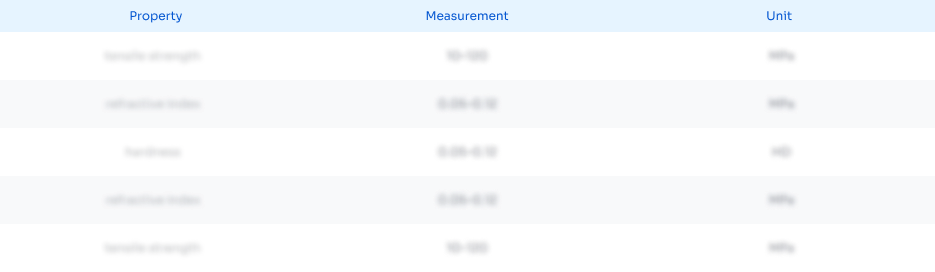
Abstract
Description
Claims
Application Information

- R&D Engineer
- R&D Manager
- IP Professional
- Industry Leading Data Capabilities
- Powerful AI technology
- Patent DNA Extraction
Browse by: Latest US Patents, China's latest patents, Technical Efficacy Thesaurus, Application Domain, Technology Topic, Popular Technical Reports.
© 2024 PatSnap. All rights reserved.Legal|Privacy policy|Modern Slavery Act Transparency Statement|Sitemap|About US| Contact US: help@patsnap.com