Production process of potassium carbonate
A production process, potassium carbonate technology, applied in the direction of carbonate preparations, etc., can solve the problems of multiple processes, low energy consumption, high energy consumption, etc., and achieve the effects of simplified process steps, lower evaporation temperature, and lower evaporation temperature
- Summary
- Abstract
- Description
- Claims
- Application Information
AI Technical Summary
Problems solved by technology
Method used
Image
Examples
Embodiment
[0022] Such as figure 1 Shown, a kind of preparation method of potassium carbonate, adopts 732 type strongly acidic cation exchange resins with potassium chloride as regeneration agent, makes eluting agent with ammonium bicarbonate, utilizes ion exchange method to obtain the mixed solution of potassium bicarbonate and ammonium bicarbonate and ammonium chloride solution.
[0023] The mixed diluted solution is evaporated at a negative pressure of 0.7Mpa and an evaporation temperature of 85°C. Since the decomposition temperature of ammonium bicarbonate is lower than that of potassium bicarbonate, only a small amount of potassium bicarbonate is converted into potassium carbonate during the evaporation process, while CO released from ammonium bicarbonate 2 The carbonization process of potassium carbonate can be completely realized, and the evaporation self-carbonization process is completed. The ammonia-containing distilled water after evaporation and self-carbonization is returne...
Embodiment 2
[0026] Such as figure 1 Shown, a kind of preparation method of potassium carbonate, adopts 732 type strongly acidic cation exchange resins with potassium chloride as regeneration agent, makes eluting agent with ammonium bicarbonate, utilizes ion exchange method to obtain the mixed solution of potassium bicarbonate and ammonium bicarbonate and ammonium chloride solution. Evaporate the mixed solution at a negative pressure of 0.6Mpa and an evaporation temperature of 75°C. Since the decomposition temperature of ammonium bicarbonate is lower than that of potassium bicarbonate, only a small amount of potassium bicarbonate is converted into potassium carbonate during the evaporation process, while the carbonic acid CO released from ammonium hydrogen 2 The carbonization process of potassium carbonate can be fully realized, and the evaporation self-carbonization process can be completed. All the other are the same with embodiment 1.
Embodiment 3
[0028] Such as figure 1 Shown, a kind of preparation method of potassium carbonate, adopts 732 type strongly acidic cation exchange resins with potassium chloride as regeneration agent, makes eluting agent with ammonium bicarbonate, utilizes ion exchange method to obtain the mixed solution of potassium bicarbonate and ammonium bicarbonate and ammonium chloride solution. Evaporate the mixed solution at a negative pressure of 0.8Mpa and an evaporation temperature of 90°C. Since the decomposition temperature of ammonium bicarbonate is lower than that of potassium bicarbonate, only a small amount of potassium bicarbonate is converted into potassium carbonate during the evaporation process, while carbonate CO released from ammonium hydrogen 2 The carbonization process of potassium carbonate can be fully realized, and the evaporation self-carbonization process can be completed. All the other are the same with embodiment 1.
PUM
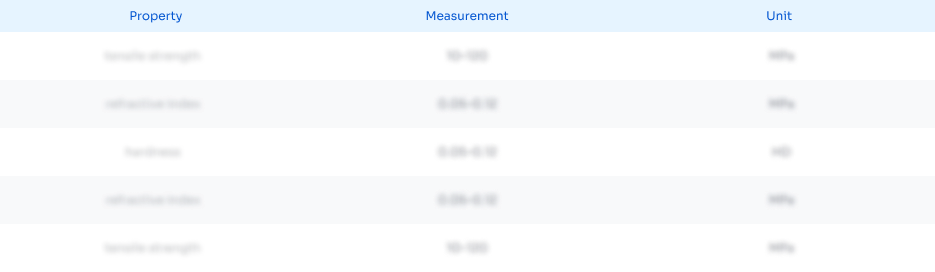
Abstract
Description
Claims
Application Information

- Generate Ideas
- Intellectual Property
- Life Sciences
- Materials
- Tech Scout
- Unparalleled Data Quality
- Higher Quality Content
- 60% Fewer Hallucinations
Browse by: Latest US Patents, China's latest patents, Technical Efficacy Thesaurus, Application Domain, Technology Topic, Popular Technical Reports.
© 2025 PatSnap. All rights reserved.Legal|Privacy policy|Modern Slavery Act Transparency Statement|Sitemap|About US| Contact US: help@patsnap.com