Process for producing high-purity hexafluoropropylene and cleaning gas
A kind of technology of hexafluoropropene and production method, which is applied in the field of production of high-purity hexafluoropropene and achieves the effect of a simple method
- Summary
- Abstract
- Description
- Claims
- Application Information
AI Technical Summary
Problems solved by technology
Method used
Image
Examples
preparation example 1
[0064] After thermal decomposition (thermal decomposition temperature 600 ° C) from chlorodifluoromethane (CHClF 2 ) When tetrafluoroethylene is produced, the product is distilled twice to recover tetrafluoroethylene, and then crude hexafluoropropylene is obtained. The crude hexafluoropropylene was analyzed by gas chromatography ["GC-14A" manufactured by Shimadzu Corporation, column: Porapack-Q (6m) manufactured by Shimadzu Corporation, measurement temperature: 80 to 200°C]. The results are shown in Table 1.
Embodiment 1
[0066] 80 g of molecular sieve 13X (manufactured by Union Showa Co., Ltd.: average pore diameter 10 , the ratio of silica / aluminum=0.81) and 70g of carbonaceous adsorbent (carbon molecular sieve 5A, manufactured by Takeda Pharmaceutical Co., Ltd.: average pore diameter ) were mixed and filled into a stainless steel cylinder with a capacity of 1000 ml, and vacuum-dried. Next, while cooling the cylinder, about 550 g of the crude hexafluoropropylene obtained in Preparation Example 1 above was filled thereinto, stirred constantly at room temperature, and the liquid phase was recovered after filling for about 12 hours [step (1)]. The liquid phase was analyzed by gas chromatography ["GC-14A" manufactured by Shimadzu Corporation, column: Porapack-Q (6m) manufactured by Shimadzu Corporation, measurement temperature: 80 to 200°C]. The results are shown in Table 1.
[0067] Next, the liquid phase obtained in the above step (1) is introduced into a distillation column, the low boiling...
reference example 1
[0069] 30 g of molecular sieve 13X (manufactured by Union Showa Co., Ltd.: average pore diameter 10 , the ratio of silica / aluminum=0.81) was filled in a stainless steel cylinder with a volume of 200 ml, and vacuum-dried. Next, while cooling the cylinder, about 70 g of the crude hexafluoropropylene obtained in Preparation Example 1 above was filled thereinto, stirred constantly at room temperature, and the liquid phase was recovered after filling for about 12 hours. The liquid phase was analyzed by gas chromatography ["GC-14A" manufactured by Shimadzu Corporation, column: Porapack-Q (6m) manufactured by Shimadzu Corporation, measurement temperature: 80 to 200°C]. The results are shown in Table 1.
PUM
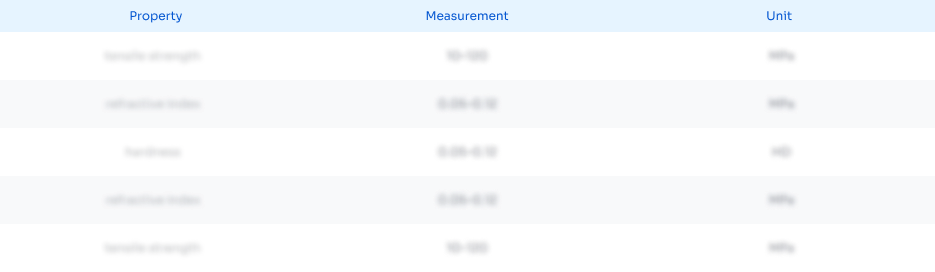
Abstract
Description
Claims
Application Information

- R&D
- Intellectual Property
- Life Sciences
- Materials
- Tech Scout
- Unparalleled Data Quality
- Higher Quality Content
- 60% Fewer Hallucinations
Browse by: Latest US Patents, China's latest patents, Technical Efficacy Thesaurus, Application Domain, Technology Topic, Popular Technical Reports.
© 2025 PatSnap. All rights reserved.Legal|Privacy policy|Modern Slavery Act Transparency Statement|Sitemap|About US| Contact US: help@patsnap.com