Stainless steel smelting method
A smelting method and stainless steel technology, applied in the field of smelting, can solve the problems of long alloy addition time, low ladle life, low production efficiency, etc., and achieve the effects of expanding forging production capacity, reducing steelmaking costs, and improving production efficiency.
- Summary
- Abstract
- Description
- Claims
- Application Information
AI Technical Summary
Problems solved by technology
Method used
Examples
Embodiment Construction
[0016] The steps of the method for smelting stainless steel of the present invention are as follows:
[0017] 1) Electric furnace smelting, tapping temperature 1670-1720℃;
[0018] 2) Intermediate frequency furnace melting alloy, melting alloy temperature: 1620-1700 ℃;
[0019] 3) LF furnace heating 1540-1620 ℃;
[0020] 4) VOD vacuum decarburization; carbon content can reach ≤0.02%
[0021] 5) VOD vacuum reduction, adding metal aluminum as a reducing agent in a vacuum state, reduction time: 10-60min, S≤0.08%;
[0022] 6) Argon protection pouring.
PUM
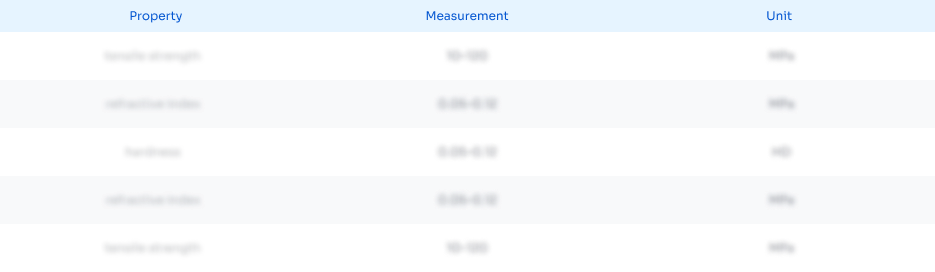
Abstract
Description
Claims
Application Information

- R&D
- Intellectual Property
- Life Sciences
- Materials
- Tech Scout
- Unparalleled Data Quality
- Higher Quality Content
- 60% Fewer Hallucinations
Browse by: Latest US Patents, China's latest patents, Technical Efficacy Thesaurus, Application Domain, Technology Topic, Popular Technical Reports.
© 2025 PatSnap. All rights reserved.Legal|Privacy policy|Modern Slavery Act Transparency Statement|Sitemap|About US| Contact US: help@patsnap.com