Numerical control gate boring-milling machine high-speed main spindle clamp tool resetting mechanism
A technology of high-speed spindle and reset mechanism, which is applied in the direction of clamping, positioning devices, metal processing machinery parts, etc., can solve the problem of high force on the thrust bearing at the tail of the spindle, and achieve high-speed re-cutting and reduce the force load.
- Summary
- Abstract
- Description
- Claims
- Application Information
AI Technical Summary
Problems solved by technology
Method used
Image
Examples
Embodiment Construction
[0014] Below in conjunction with accompanying drawing, the utility model is further described:
[0015] attached by Figure 4 - attached Figure 6 As shown, the high-speed spindle tool clamping reset mechanism of the CNC gantry boring and milling machine is improved on the basis of the original mechanism, and the oil chamber c for realizing the reset action is added, so that there is a tool clamping reset gap X between the push rod 8 and the spindle sleeve 7, The value range of X is between 1mm and 3mm, which is sufficient to ensure that the push rod 8 is separated from the main shaft sleeve 7, and if it is too large, the movement stroke of the tool release device will be increased. Current institutions such as Figure 4 As shown, it mainly includes oil cylinder 1, new piston rod 2 and piston 3, the left end of oil cylinder 1 is fixed with connecting sleeve 5, and the connecting sleeve 5 is fixed on the headstock of the ram; the inner steps of connecting sleeve 5, oil cylind...
PUM
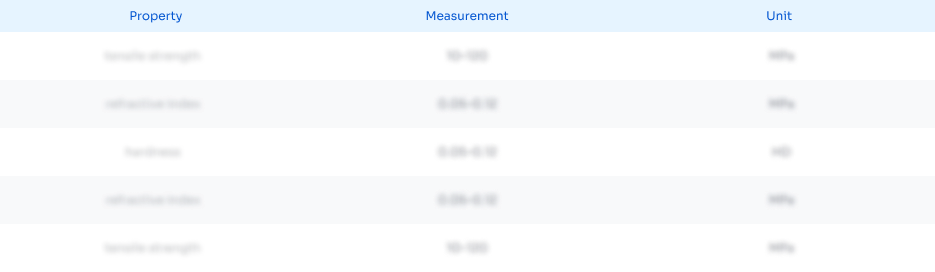
Abstract
Description
Claims
Application Information

- R&D
- Intellectual Property
- Life Sciences
- Materials
- Tech Scout
- Unparalleled Data Quality
- Higher Quality Content
- 60% Fewer Hallucinations
Browse by: Latest US Patents, China's latest patents, Technical Efficacy Thesaurus, Application Domain, Technology Topic, Popular Technical Reports.
© 2025 PatSnap. All rights reserved.Legal|Privacy policy|Modern Slavery Act Transparency Statement|Sitemap|About US| Contact US: help@patsnap.com