Microwave combustion synthesizing method for bulk nanocrystalline alloy
A nanocrystalline alloy and microwave combustion technology, which is applied in the field of microwave combustion synthesis of bulk nanocrystalline alloys, can solve the problems of high cost of nanocrystalline materials, unsatisfactory thermal stability, and uneven structure, and achieve fine and Uniformity, improvement of room temperature brittleness, and the effect of fully dense products
- Summary
- Abstract
- Description
- Claims
- Application Information
AI Technical Summary
Problems solved by technology
Method used
Image
Examples
Embodiment 1
[0017] Example 1. Synthesis of Fe-Al bulk nano-alloys by microwave combustion.
[0018] According to the composition design, high-purity Al powder and high-purity Fe powder were weighed according to Table 1, and the above powders were mixed with a high-energy ball mill. After 8 hours, the powder was taken out and put into a steel mold for cold pressing at a pressure of 100Mpa. Put the pressed billets into crucibles respectively, place them in a microwave oven for heating, select a microwave heating power of 650W, and heat for 2 minutes. During the combustion synthesis process, a reaction occurs:
[0019] Fe+Al=FeAl or
[0020] 3Fe+Al=Fe 3 Al
[0021] The product was removed after cooling to room temperature.
[0022] Fe can also be used 2 o 3 Al powder is mixed with high-purity Al powder and prepared in the same way as above. During the microwave combustion synthesis process, the reaction occurs:
[0023] Fe 2 o 3 +4Al=2FeAl+Al 2 o 3 or
[0024] 3Fe 2 o 3 +8Al=2F...
Embodiment 2
[0029] Example 2. Synthesis of Fe-Al-B bulk nano-alloys using microwave combustion.
[0030] According to needs, the required non-metallic powder can also be added to the raw material, such as preparing Fe-Al-B bulk nano-alloy, B powder can be added on the basis of metal powder. Weigh the high-purity Fe powder, high-purity Al powder and B powder according to Table 2, adopt the technological process in Example 1, the powder mixing time is 10 hours, the pressing pressure is 100MPa, the microwave power is 700W, and the heating time is 3 minutes. Fe-Al-B bulk nanocrystalline alloys with different compositions can be prepared.
[0031] Table 2 Composition of Example 2 Fe-Al-B alloy
[0032]
Embodiment 3
[0033] Example 3. Synthesis of Fe-Al-Cu bulk nano-alloys by microwave combustion.
[0034] According to the composition design, high-purity Fe powder, high-purity Al powder and Cu powder were weighed according to Table 3, and Fe-Al-Cu bulk nanocrystalline alloys with different compositions were prepared according to the above process. The powder mixing time in the process is 12 hours, the pressing pressure is 100MPa, the microwave power is 750W, and the heating time is 3 minutes.
[0035] Table 3 Composition of Example 3 Fe-Al-Cu alloy
[0036]
PUM
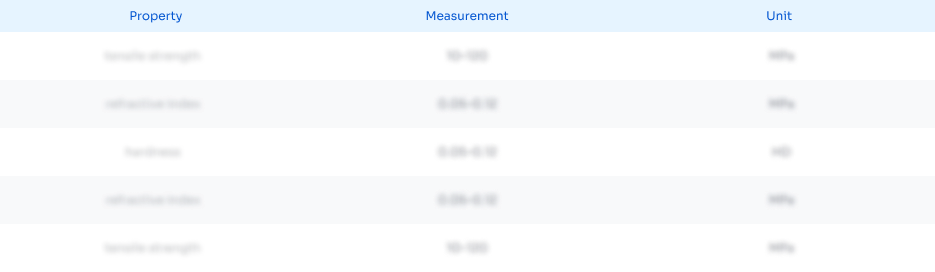
Abstract
Description
Claims
Application Information

- R&D
- Intellectual Property
- Life Sciences
- Materials
- Tech Scout
- Unparalleled Data Quality
- Higher Quality Content
- 60% Fewer Hallucinations
Browse by: Latest US Patents, China's latest patents, Technical Efficacy Thesaurus, Application Domain, Technology Topic, Popular Technical Reports.
© 2025 PatSnap. All rights reserved.Legal|Privacy policy|Modern Slavery Act Transparency Statement|Sitemap|About US| Contact US: help@patsnap.com