Membrane stress control method
A control method and film stress technology, applied in the field of spacecraft thermal control, can solve problems such as failure, wrinkle deformation, thermal control performance degradation of thermal control devices, etc., and achieve the effect of strong adaptability, wide applicability, and broad application prospects
- Summary
- Abstract
- Description
- Claims
- Application Information
AI Technical Summary
Problems solved by technology
Method used
Image
Examples
Embodiment 1
[0020] 1. Using magnetron sputtering film deposition technology to deposit a layer of tin with a thickness of about 50nm on a polyimide film with a thickness of 13um, the film deposition conditions are: the substrate temperature is room temperature, the purity of the aluminum target and the tin target Both are 99.99%, and the background vacuum is better than 3.5×10 -3 Pa, argon partial pressure is 0.4 Pa, sputtering voltage is 300V, sputtering current is 0.2A, sputtering power is 80W, and target / base spacing is 70mm.
[0021] 2. Deposit a layer of aluminum film with a thickness of 150nm on the tin layer completed in step 1. The film deposition conditions are: the substrate temperature is room temperature, the purity of the aluminum target and the tin target are both 99.99%, and the background vacuum is better than 3.0×10 -3 Pa, argon partial pressure is 0.5Pa, sputtering voltage is 400V, sputtering current is 0.4A, sputtering power is 120W, aluminum film deposition rate is 35.7nm / ...
Embodiment 2
[0024] 1. Using magnetron sputtering film deposition technology to deposit a layer of tin with a thickness of about 80 nm on a polyimide film with a thickness of 25um. The film deposition conditions are: the substrate temperature is room temperature, the purity of the aluminum target and the tin target are both 99.99%, and the background vacuum is better than 3.5×10 -3 Pa, argon partial pressure is 0.3Pa, sputtering voltage is 3500V, sputtering current is 0.25A, sputtering power is 150W, target / base spacing is 90mm;
[0025] 2. Deposit another layer of 200nm thick aluminum film on the tin layer completed in step 1. The film deposition conditions are: the substrate temperature is room temperature, the purity of the aluminum target and the tin target are both 99.99%, and the background vacuum is better than 3.5×10 -3 Pa, argon partial pressure is 0.4Pa, sputtering voltage is 400V, sputtering current is 0.2A, sputtering power is 80W, aluminum film deposition rate is 35.7nm / min, targe...
Embodiment 3
[0028] 1. Using magnetron sputtering film deposition technology to deposit a layer of tin with a thickness of about 100 nm on a polyimide film with a thickness of 25um. The film deposition conditions are: the substrate temperature is room temperature, the purity of the aluminum target and the tin target are both 99.99%, and the background vacuum is better than 3.5×10 -3 Pa, argon partial pressure is 0.5Pa, sputtering voltage is 450V, sputtering current is 0.6A, sputtering power is 180W, target / base spacing is 85mm;
[0029] 2. Deposit another layer of 200nm thick aluminum film on the tin layer completed in step 1. The film deposition conditions are: the substrate temperature is room temperature, the purity of the aluminum target and the tin target are both 99.99%, and the background vacuum is better than 3.5×10 -3 Pa, argon partial pressure is 0.3Pa, sputtering voltage is 400V, sputtering current is 0.2A, sputtering power is 80W, target / base spacing is 70mm;
[0030] 3. Place the ...
PUM
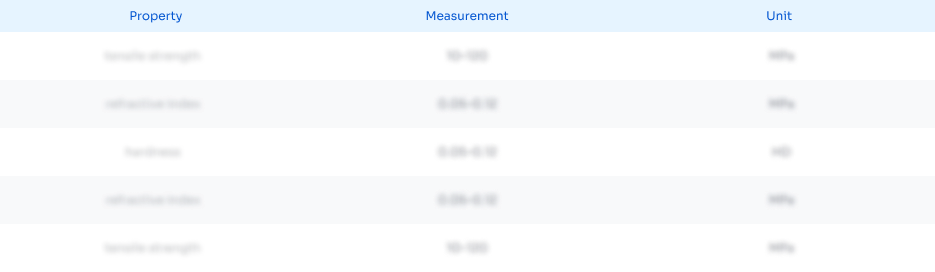
Abstract
Description
Claims
Application Information

- Generate Ideas
- Intellectual Property
- Life Sciences
- Materials
- Tech Scout
- Unparalleled Data Quality
- Higher Quality Content
- 60% Fewer Hallucinations
Browse by: Latest US Patents, China's latest patents, Technical Efficacy Thesaurus, Application Domain, Technology Topic, Popular Technical Reports.
© 2025 PatSnap. All rights reserved.Legal|Privacy policy|Modern Slavery Act Transparency Statement|Sitemap|About US| Contact US: help@patsnap.com