High-content red phosphorus flame-retardant master batch
A flame retardant masterbatch, high-content technology, applied in the field of high-content red phosphorus flame retardant masterbatch, to improve the quality of finished products, reduce product costs, and improve the production environment
- Summary
- Abstract
- Description
- Claims
- Application Information
AI Technical Summary
Problems solved by technology
Method used
Examples
Embodiment 1
[0042] First prepare raw materials by following weight ratio:
[0043] LDPE 10g
[0044] Red phosphorus 70g
[0045] Zinc borate 20g
[0046] white oil 2g
[0047] N,N'-ethylene bisstearamide 2g
[0048] Blue powder 2g
[0049] Black Powder 4g
[0050] Then, uniformly mix the materials according to the above ratio, then extrude and granulate for 15 minutes with a twin-screw granulator at 90-100°C to obtain the high-content red phosphorus flame-retardant masterbatch of the present invention.
[0051] Take 8g of the flame retardant masterbatch and add it to 100g of low-density polyethylene, and the oxygen index of the prepared flame retardant polyethylene can reach 29. However, the oxygen index of the flame-retardant polyethylene prepared with the same weight ratio of low-content red phosphorus flame-retardant masterbatch is only 25.
Embodiment 2
[0053] First prepare raw materials by following weight ratio:
[0054] Polyamide 10g
[0055] Red phosphorus 50g
[0056] Melamine cyanurate 40g
[0057] white oil 2g
[0058] N,N'-ethylene bisstearamide 2g
[0059] Blue powder 2g
[0060] Black powder 1g
[0061]Then, uniformly mix the materials according to the above ratio, then extrude and granulate for 10 minutes with a twin-screw granulator at 120-130°C to obtain the high-content black red phosphorus flame-retardant masterbatch of the present invention.
[0062] Add 8 g of the flame retardant masterbatch to 100 g of polyamide, and the obtained black flame retardant polyamide has an oxygen index of up to 38, and processing does not require coloring. However, the oxygen index of the flame-retardant polyamide prepared with the same weight ratio of low-content red phosphorus flame-retardant masterbatch is only 31.
Embodiment 3
[0064] First prepare raw materials by following weight ratio:
[0065] Polypropylene 10g
[0066] Red phosphorus 90g
[0067] Magnesium hydroxide 10g
[0068] Triphenyl Phosphate 1g
[0069] N,N'-ethylene bisstearamide 2g
[0070] Then, uniformly mix the materials according to the above ratio, extrude and granulate for 8 minutes with a twin-screw granulator at 140-150°C to obtain the high-content red phosphorus flame-retardant masterbatch of the present invention.
[0071] Take 8g of the flame retardant masterbatch and add it to 100g polypropylene, and the oxygen index of the prepared flame retardant polypropylene can reach 29. However, the oxygen index of flame-retardant polypropylene prepared with the same weight ratio of low-content red phosphorus flame-retardant masterbatch is only 24.
PUM
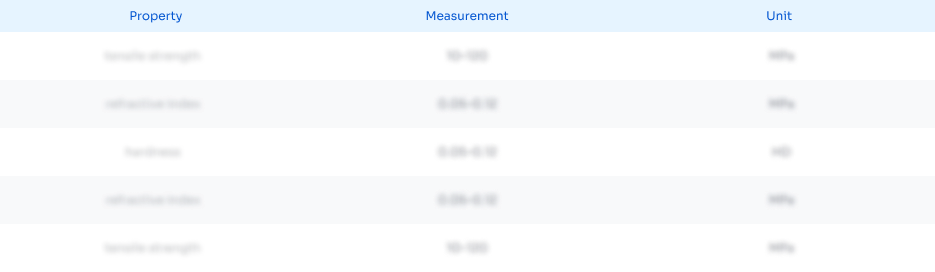
Abstract
Description
Claims
Application Information

- Generate Ideas
- Intellectual Property
- Life Sciences
- Materials
- Tech Scout
- Unparalleled Data Quality
- Higher Quality Content
- 60% Fewer Hallucinations
Browse by: Latest US Patents, China's latest patents, Technical Efficacy Thesaurus, Application Domain, Technology Topic, Popular Technical Reports.
© 2025 PatSnap. All rights reserved.Legal|Privacy policy|Modern Slavery Act Transparency Statement|Sitemap|About US| Contact US: help@patsnap.com