Voltage increasing subsection heating high-temperature erosion abrasion machine
A technology of wear test and segmental heating, which is applied in the direction of testing wear resistance, etc., and can solve problems such as increased wear speed and high temperature oxidation
- Summary
- Abstract
- Description
- Claims
- Application Information
AI Technical Summary
Problems solved by technology
Method used
Image
Examples
Embodiment Construction
[0017] As shown in Figures 1 and 2, this embodiment includes a high-temperature air heating furnace 3, a closed abrasive feeder 5, a sample heating erosion device 6, an erosion gas delivery pipeline 2, a high-pressure gas storage tank 9, an air supply System 1. The inlet end of the erosion gas delivery pipeline 2 is connected to the outlet end of the high-pressure gas storage tank 9, the inlet end of the high-pressure gas storage tank 9 is connected to the air supply system 1, and the other outlet end of the high-pressure gas storage tank 9 is connected to the closed grinding mill. The upper cavity of the material bin of the grain feeder 5 is connected, and the erosion gas delivery pipeline 2 runs through the high-temperature air heating furnace 3, and then passes into the sample heating erosion device 6, and the outlet of the erosion gas delivery pipeline 2 points to be placed vertically on the sample Heating the middle of the sample block in the erosion device 6 and forming ...
PUM
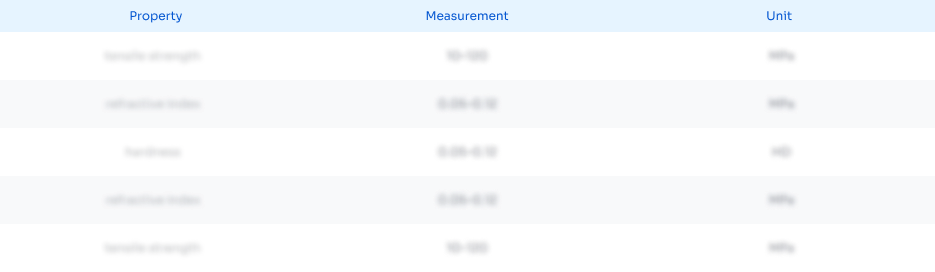
Abstract
Description
Claims
Application Information

- R&D Engineer
- R&D Manager
- IP Professional
- Industry Leading Data Capabilities
- Powerful AI technology
- Patent DNA Extraction
Browse by: Latest US Patents, China's latest patents, Technical Efficacy Thesaurus, Application Domain, Technology Topic, Popular Technical Reports.
© 2024 PatSnap. All rights reserved.Legal|Privacy policy|Modern Slavery Act Transparency Statement|Sitemap|About US| Contact US: help@patsnap.com