Continuous pad dyeing method of polyamide fibers and blended fabrics thereof
A technology of blended fabrics and nylon, applied in the field of continuous pad dyeing of nylon and its blended fabrics, can solve the problems of batch difference and low dyeing efficiency of exhaust dyeing, and achieve the effect of ensuring color fastness, good use value and color yield
- Summary
- Abstract
- Description
- Claims
- Application Information
AI Technical Summary
Problems solved by technology
Method used
Examples
Embodiment 1
[0022] 1. Pretreatment of nylon / cotton blended fabric
[0023] Process: brocade / cotton interwoven fabric-singeing-cold pad-batch-mercerizing-pre-setting.
[0024] ① Use 50 / 50 nylon-cotton blended fabric.
[0025] ②The singeing process is fast singeing with one front and one reverse, and the speed is 140m / min.
[0026] ③The process of cold pad-batch is two dipping and two rolling, and it is rotated and stacked for 24 hours.
[0027] Dye liquor process prescription (final concentration):
[0028] Caustic soda 40g / L
[0029] Hydrogen peroxide 20g / L
[0031] Penetrant JFC 2~3g / L
[0032] Chelating agent X-178 2g / L
[0033] Deyouling TF-101C 2~4g / L
[0034] The solvent is water.
[0035] ④ Mercerized
[0036] Treatment solution prescription ():
[0037] Caustic soda 210~220g / L
[0038] The solvent is water.
[0039] ⑤Pre-setting process: The setting temperature is 150~160℃×30min.
[0040] 2. Dyeing of brocade / cotton blended fabric
[004...
Embodiment 2
[0067] According to the method steps described in Example 1, the difference is that the process of first rolling reactive dyes and then rolling acid dyes is adopted, and other process parameters are constant, and the flow process is as follows:
[0068] Conventional rolling of reactive dyes→set rolling of acid dye solution (one soaking and one rolling, hot rolling 65~70°C)→infrared pre-baking→first drying room (80°C)→second drying room (100°C)→falling cloth→dipping Color fixing solution (one soaking and one rolling, room temperature)→steaming (steaming temperature 103°C, time 90 seconds)→cold water washing→second color fixing (70~80°C)→water washing→drying.
[0069] The nylon / cotton blended fabric treated above is dark brown, and the color fastness to rubbing of the fabric is evaluated according to GB / T3920-1997, among which the dry rubbing resistance is 4~5, and the wet rubbing resistance is 4, and the fabric is evaluated according to GB / T3921-1997 The color fastness to washi...
Embodiment 3
[0071] According to the dyeing method described in Implementation 1, the difference is that the 50 / 50 nylon-cotton interwoven fabric is replaced by pure nylon fabric, and the conventional reactive dye solution step is omitted, and the acid dye prescription is replaced by the following components:
[0072] Weak acid yellow B-4R 3g / L
[0073] Red A-2B 3g / L
[0074] Blue B-N2RL 4g / L
[0075] The solvent is water.
[0076] After drying, a light brown nylon fabric can be obtained. The color fastness to rubbing of the fabric is evaluated according to GB / T3920-1997, among which the resistance to dry rubbing is 4 to 5, and the resistance to wet rubbing is 4. The color fastness to rubbing of the fabric is evaluated according to GB / T3921-1997. Color fastness to washing (60°C), among which the color fastness to fading is grade 4-5, and the color fastness to staining is grade 4.
PUM
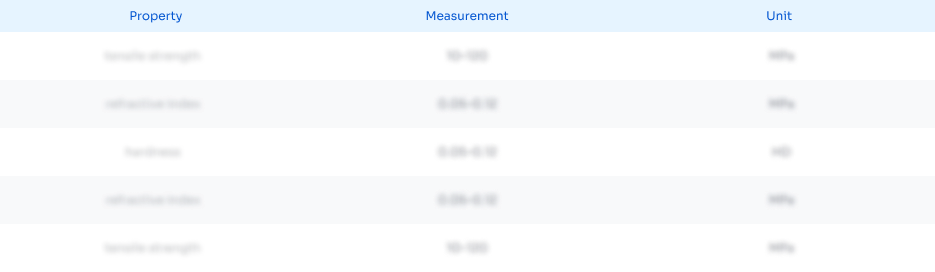
Abstract
Description
Claims
Application Information

- R&D
- Intellectual Property
- Life Sciences
- Materials
- Tech Scout
- Unparalleled Data Quality
- Higher Quality Content
- 60% Fewer Hallucinations
Browse by: Latest US Patents, China's latest patents, Technical Efficacy Thesaurus, Application Domain, Technology Topic, Popular Technical Reports.
© 2025 PatSnap. All rights reserved.Legal|Privacy policy|Modern Slavery Act Transparency Statement|Sitemap|About US| Contact US: help@patsnap.com