High flow flat imitating steam mold UV curing coating and production method, construction method
A technology of curing paint and steam mold, applied in the direction of coating, device for coating liquid on the surface, surface pretreatment, etc. It can solve the problem of high cost of injection molding equipment, poor surface scratch resistance, and inability to achieve the appearance of the shell. And other issues
- Summary
- Abstract
- Description
- Claims
- Application Information
AI Technical Summary
Problems solved by technology
Method used
Examples
Embodiment 1
[0099] 50% solids thermoplastic acrylic resin 9;
[0100] High molecular weight block copolymer solution with pigment affinity groups 1;
[0101] Ethylene glycol butyl ether 6;
[0102] Ethylene glycol methyl ether acetate 7;
[0103] Butyl acetate 3;
[0104] Carbon black 2.5;
[0105] 35% solid thermoplastic acrylic resin solution 50;
[0106] Containing 30% vinyl chloride terpolymer resin solution 8;
[0107] Containing 15% cellulose acetate butyrate resin solution 10;
[0108] Polyester resin 0.5;
[0109] Cyclohexanone 3;
Embodiment 2
[0111] 50% solids thermoplastic acrylic resin 12;
[0112] High molecular weight block copolymer solution with pigment affinity groups 1.5;
[0113] Ethylene glycol butyl ether 6;
[0114] Ethylene glycol methyl ether acetate 6;
[0115] Butyl acetate 2.5;
[0116] carbon black 3;
[0117] 35% solids thermoplastic acrylic resin solution 45;
[0118] Containing 30% vinyl chloride terpolymer resin solution 10;
[0119] Containing 15% cellulose acetate butyrate resin solution 11;
[0120] polyester resin 1;
[0121] Cyclohexanone 2;
Embodiment 3
[0123] 50% solids thermoplastic acrylic resin 14;
[0124] High molecular weight block copolymer solution with pigment affinity groups 2;
[0125] Ethylene glycol butyl ether 5;
[0126] Ethylene glycol methyl ether acetate 5;
[0127] Butyl acetate 2;
[0128] Carbon black 3.5;
[0129] 35% solids thermoplastic acrylic resin solution 35;
[0130] Containing 30% vinyl chloride terpolymer resin solution 10;
[0131] Containing 15% cellulose acetate butyrate resin solution 20;
[0132] Polyester resin 2.5;
[0133] Cyclohexanone 1;
PUM
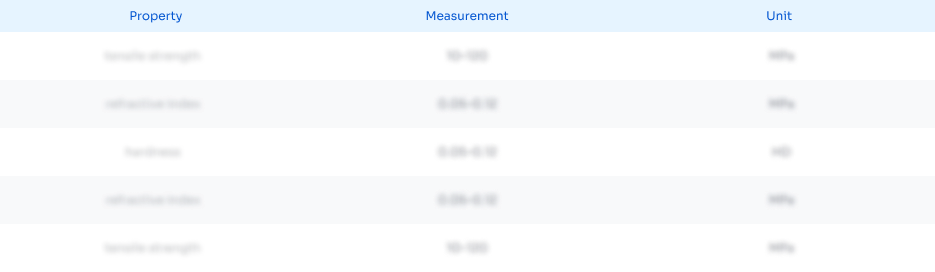
Abstract
Description
Claims
Application Information

- R&D
- Intellectual Property
- Life Sciences
- Materials
- Tech Scout
- Unparalleled Data Quality
- Higher Quality Content
- 60% Fewer Hallucinations
Browse by: Latest US Patents, China's latest patents, Technical Efficacy Thesaurus, Application Domain, Technology Topic, Popular Technical Reports.
© 2025 PatSnap. All rights reserved.Legal|Privacy policy|Modern Slavery Act Transparency Statement|Sitemap|About US| Contact US: help@patsnap.com