Porous propping agent combination and preparation method thereof
A technology of proppant and composition, which is applied in the field of porous proppant composition and its preparation in the hydroprocessing process, can solve the problems of large temperature rise of the catalyst bed and difficult control of the catalyst activation process, and achieve shortened start-up time, suitable Suitable for large-scale use and low production cost
- Summary
- Abstract
- Description
- Claims
- Application Information
AI Technical Summary
Problems solved by technology
Method used
Image
Examples
Embodiment 1
[0037] The preparation process of porous proppant composition CA1 is as follows:
[0038] The molten elemental sulfur is introduced into the alumina porous proppant SA1, and the amount of elemental sulfur introduced is 180% of the weight of the porous proppant. Then tetrabutylthiuram disulfide (TBTD) is mixed with heavy diesel oil, and this mixture is introduced in the catalyst containing elemental sulfur by impregnation method, and the TBTD consumption is 3% of porous proppant weight, and heavy diesel oil consumption is porous proppant 20% by weight. Finally, the porous proppant composition CA1 was obtained by treating at 160° C. for 5 hours in a normal-pressure, non-flowing air atmosphere.
Embodiment 2
[0040] The preparation process of porous proppant composition CA2 is as follows:
[0041] Disperse tetramethylthiuram disulfide (TMTD) in an organic solvent (a mixture of peanut oil and heavy diesel oil at a weight ratio of 4:1), disperse elemental sulfur in the above mixture, and introduce the mixture into the porous proppant SA2 by impregnation Among them, the introduction amount of elemental sulfur is 60% of the weight of the porous proppant, the amount of TMTD is 2% of the weight of the porous proppant, and the amount of organic solvent is 15% of the weight of the porous proppant. Finally, the porous proppant composition CA2 was obtained by treating at 160° C. for 5 hours in a normal-pressure, non-flowing air atmosphere.
Embodiment 3
[0043] The preparation process of porous proppant composition CA3 is as follows:
[0044] The molten elemental sulfur is introduced into the alumina porous proppant SA3 by impregnation, and the amount of elemental sulfur introduced is 270% of the weight of the porous proppant. Then tetramethylthiuram disulfide (TMTD) is dissolved in benzene, and the mixture is introduced into the catalyst containing elemental sulfur by impregnation method, and the amount of TMTD is 5% of the weight of the porous proppant. Finally, the porous proppant composition CA3 was obtained by treating at 120° C. for 5 hours under normal pressure, in an atmosphere with a volume ratio of water vapor and air of 5:1.
PUM
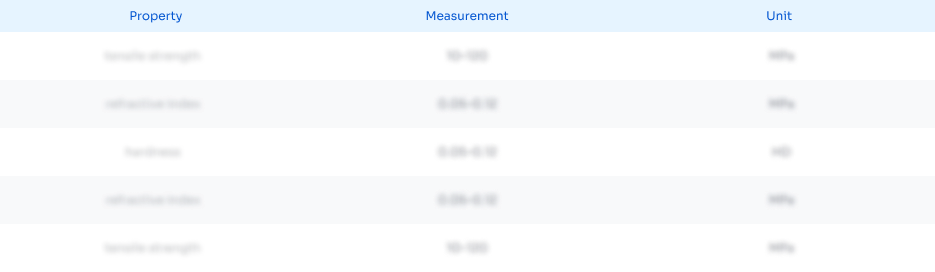
Abstract
Description
Claims
Application Information

- R&D
- Intellectual Property
- Life Sciences
- Materials
- Tech Scout
- Unparalleled Data Quality
- Higher Quality Content
- 60% Fewer Hallucinations
Browse by: Latest US Patents, China's latest patents, Technical Efficacy Thesaurus, Application Domain, Technology Topic, Popular Technical Reports.
© 2025 PatSnap. All rights reserved.Legal|Privacy policy|Modern Slavery Act Transparency Statement|Sitemap|About US| Contact US: help@patsnap.com