Once-through method of aluminum-plating film resin transfer printing
A technology of transfer printing and aluminized film, which is applied in dyeing, textiles and papermaking, etc. It can solve the problems of pollution, rough pattern surface, poor gloss, etc., and achieve the effect of strong gloss, clear transfer pattern and rich colors
- Summary
- Abstract
- Description
- Claims
- Application Information
AI Technical Summary
Problems solved by technology
Method used
Examples
Embodiment Construction
[0011] The one-time method of aluminized film resin transfer printing of the present invention is to melt polyethylene hot-melt resin into a liquid at 120°C, and then use a gravure printing machine with a heating insulation tank and an inner heating roller to keep the resin in a molten state. The pattern is printed on the aluminum layer of the colorful aluminized film, and the aluminized film is rolled up after cooling to room temperature for later use. When printing, stick the aluminized film with the polyethylene hot-melt resin pattern on the substrate, emboss at 85°C to 120°C, and peel off the film after cooling to become a finished product. The embossing described above includes the embossing of the roll material, or the embossing of the flat material.
[0012] In the present invention, the hot-melt resin can also use polyvinyl chloride or polyamide resin and other resins. During thermal transfer printing, the melting temperature of the resin should be adjusted according t...
PUM
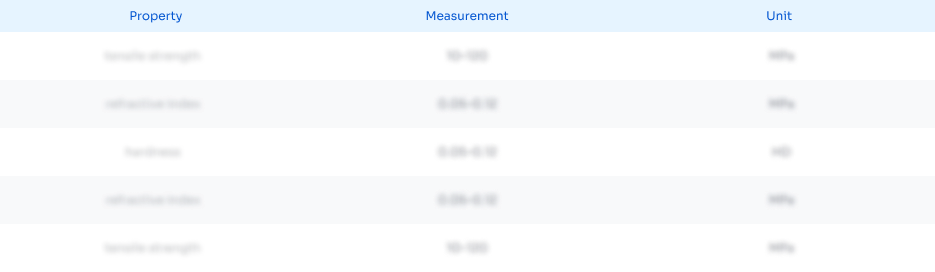
Abstract
Description
Claims
Application Information

- R&D Engineer
- R&D Manager
- IP Professional
- Industry Leading Data Capabilities
- Powerful AI technology
- Patent DNA Extraction
Browse by: Latest US Patents, China's latest patents, Technical Efficacy Thesaurus, Application Domain, Technology Topic, Popular Technical Reports.
© 2024 PatSnap. All rights reserved.Legal|Privacy policy|Modern Slavery Act Transparency Statement|Sitemap|About US| Contact US: help@patsnap.com