Wear resistant copper-based gradient material for manufacturing pantograph slider and preparation thereof
A technology of gradient materials and pantograph slides, applied in chemical instruments and methods, current collectors, electric vehicles, etc., can solve the problems of low service life, short service life, easy local grooves, etc., and achieve excellent friction and wear performance, high Mechanical strength and electrical conductivity, the effect of simple preparation process
- Summary
- Abstract
- Description
- Claims
- Application Information
AI Technical Summary
Problems solved by technology
Method used
Examples
Embodiment 1
[0011] a. Add 97 grams of copper and 3 grams of zirconia into the ball mill, put 400 grams of balls into it, mix at a speed of 400r / min for 3 hours, and mix well for later use; then add 85 grams of copper and 15 grams of graphite into the ball mill , put in 300 grams of grinding balls, mix at a speed of 400r / min for 3 hours, mix well and set aside.
[0012] b. Add the uniformly mixed copper-zirconia powder into the grinding tool, and vibrate evenly; add 20 grams of pure copper powder on the top of the copper-zirconia in the grinding tool, and vibrate evenly; then add uniformly mixed copper on the pure copper layer - Graphite powder 80 g. The mold is put into a cold isostatic press and pressed at 500MPa.
[0013] c. Take out the pressed and formed material from the mold, and put it in a vacuum of 10 -4 MPa, heated to a temperature of 860°C at a heating rate of 10°C / min, held for 5 hours for sintering, and then cooled to room temperature. A copper-based gradient wear-resistan...
Embodiment 2
[0015] a. Add 80 grams of copper and 20 grams of zirconia into the ball mill, put 400 grams of balls into it, mix at a speed of 250r / min for 4 hours, and mix well for later use; then add 90 grams of copper and 10 grams of graphite into the ball mill , put in 400 grams of grinding balls, mix at a speed of 250r / min for 4 hours, mix well and set aside.
[0016] b. Add the uniformly mixed copper-zirconia powder into the grinding tool and vibrate evenly; add 20 grams of pure copper powder on top of the copper-zirconia in the mold and vibrate evenly; then add uniformly mixed copper powder on the pure copper powder layer - Graphite powder 80 g. The mold is put into a cold isostatic press and pressed at 400MPa.
[0017] c. Take out the pressed and formed material from the mold, and put it in a vacuum of 10 -4 MPa, heated to a temperature of 450°C at a heating rate of 10° / min, and then to a temperature of 900°C at a heating rate of 15° / min, held for 4 hours for sintering, and then co...
Embodiment 3
[0019] a. Add 90 grams of copper and 10 grams of zirconia into the ball mill, put 400 grams of balls into it, mix at a speed of 350r / min for 4 hours, and mix well for later use; then add 95 grams of copper and 5 grams of graphite into the ball mill , put in 400 grams of grinding balls, mix at a speed of 350r / min for 5 hours, mix well and set aside.
[0020] b. Add uniformly mixed copper-zirconia powder into the mold and vibrate evenly; add 20 grams of pure copper powder above the copper-zirconia in the mold and vibrate evenly; then add uniformly mixed copper-graphite on the pure copper layer Powder 80 grams. The mold is put into a cold isostatic press and pressed at 600MPa.
[0021] c. Take out the press-molded material from the mould, and place it in a vacuum of 10 -4 MPa, heated to a temperature of 550°C at a heating rate of 10° / min, and then to a temperature of 960°C at a heating rate of 15° / min, held for 3 hours for sintering, and then cooled to room temperature. A copp...
PUM
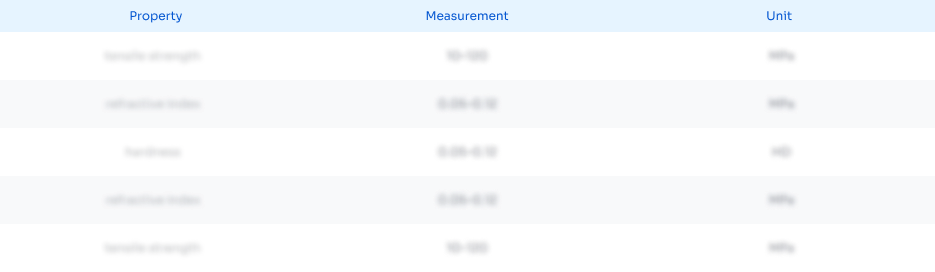
Abstract
Description
Claims
Application Information

- R&D
- Intellectual Property
- Life Sciences
- Materials
- Tech Scout
- Unparalleled Data Quality
- Higher Quality Content
- 60% Fewer Hallucinations
Browse by: Latest US Patents, China's latest patents, Technical Efficacy Thesaurus, Application Domain, Technology Topic, Popular Technical Reports.
© 2025 PatSnap. All rights reserved.Legal|Privacy policy|Modern Slavery Act Transparency Statement|Sitemap|About US| Contact US: help@patsnap.com