Method for processing turbine runner shaft
A processing method and turbine shaft technology, which is applied in the processing field of turbine shafts, can solve problems such as inconsistent tool wear, tool damage, and mass center offset, and achieve the effect of beautiful appearance and improved pass rate
- Summary
- Abstract
- Description
- Claims
- Application Information
AI Technical Summary
Problems solved by technology
Method used
Image
Examples
Embodiment 1
[0020] Embodiment 1: as shown in Fig. 1, Fig. 2 and Fig. 3, a kind of machining method of turbine shaft comprises the following steps: (1) rough turning the outer circle, light out the small end of the optical axis 1 and punch the center hole 2; (2) Coarse dynamic balance; (3) Correct the optical axis central hole 2 and the turbine end central hole 3 by eccentricity according to the coarse dynamic balance; (4) Take the corrected optical axis central hole 2 and the turbine end central hole 3 as the reference vehicle The outer circle of the optical axis is 6, the total length of the optical axis is taken with the center frame, and the center hole of the optical axis is re-drilled; (5) The center hole of the optical axis is used to semi-finish the outer circle of each level of semi-finishing; (6) Heat treatment and annealing; (7) Grinding Cutting the outer circle and end face of the turbine; (8) flaw detection inspection; (9) processing R groove 8 at the root of the turbine shaft;...
PUM
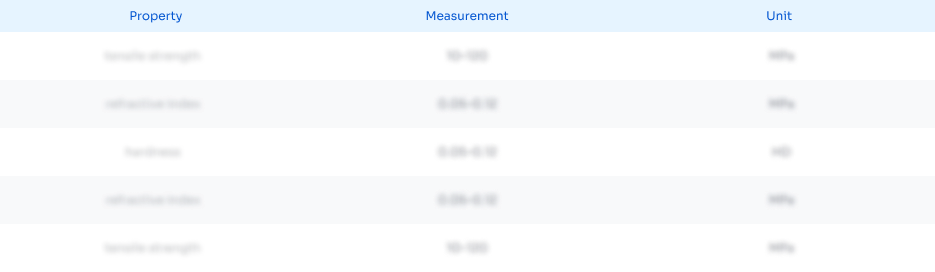
Abstract
Description
Claims
Application Information

- R&D
- Intellectual Property
- Life Sciences
- Materials
- Tech Scout
- Unparalleled Data Quality
- Higher Quality Content
- 60% Fewer Hallucinations
Browse by: Latest US Patents, China's latest patents, Technical Efficacy Thesaurus, Application Domain, Technology Topic, Popular Technical Reports.
© 2025 PatSnap. All rights reserved.Legal|Privacy policy|Modern Slavery Act Transparency Statement|Sitemap|About US| Contact US: help@patsnap.com