Method for preparing cucr 40 contact material by vacuum casting method
A technology for electrical contacts and vacuum furnaces, which is applied in the field of CuCr 40 electrical contacts prepared by vacuum melting and casting, which can solve the problems of difficult process stability, poor toughness, and large particle size of CuCr40
- Summary
- Abstract
- Description
- Claims
- Application Information
AI Technical Summary
Problems solved by technology
Method used
Image
Examples
Embodiment 1
[0022] Weigh 2.24kg of Cr block, under the protection of low-temperature liquid, process it into Cr powder by grinding and crushing machine, control the powder-making temperature below -100°C, press Cr powder, and sinter at 1300°C for 1 hour to make Cr powder blank , and then weigh 3.36Kg of Cu block and Cr powder into a vacuum furnace, at P≤8×10 -2 Heating at a speed of 80°C / min under a vacuum of Pa, when the temperature rises to 1800°C for 5 minutes, rapid casting. After cooling, the CuCr40 electrical contact material is obtained.
Embodiment 2
[0024] Weigh 2.24 kg of Cr block under the protection of low-temperature liquid, and process it into Cr powder by grinding and crushing machine. The powder-making temperature is controlled at -100°C. After the Cr powder is pressed, it is sintered at 1350°C for 2 hours to make Cr powder. Then weigh 3.36kg of Cu block and put it into a vacuum furnace with Cr powder, at P≤8×10 -2 Heating at a speed of 80°C / min under a vacuum of Pa, when the temperature rises to 1900°C and keeps for 5 minutes, rapid casting. After cooling, the CuCr40 electrical contact material is obtained.
Embodiment 3
[0026] Weigh 2.24kg of Cr block under the protection of low-temperature liquid, and process it into Cr powder by grinding and crushing machine. The powder-making temperature is controlled at -100°C. After the Cr powder is pressed, it is sintered at 1400°C for 3 hours to make Cr powder. Then weigh 3.36kg of Cu block and put it into a vacuum furnace with Cr powder, at P≤8×10 -2 Heating at a speed of 80°C / min under a vacuum of Pa, when the temperature rises to 2000°C and keeps for 5 minutes, rapid casting. After cooling, the CuCr40 electrical contact material is obtained.
[0027] The composite material prepared by the invention has excellent comprehensive properties. The performance comparison between the prepared CuCr40 composite material and the infiltration method CuCr40 composite material is shown in Table 1.
[0028] Table 1 Performance comparison of CuCr40 composites
[0029]
PUM
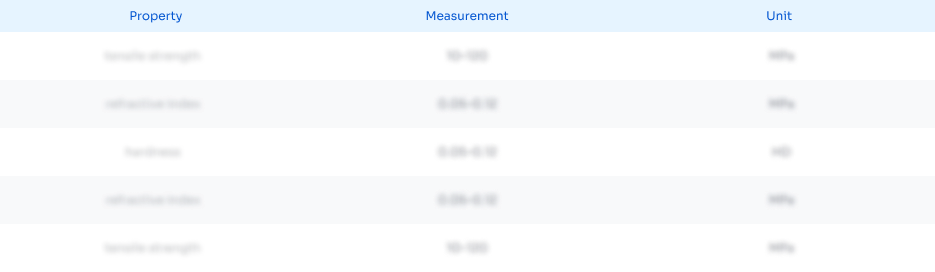
Abstract
Description
Claims
Application Information

- R&D
- Intellectual Property
- Life Sciences
- Materials
- Tech Scout
- Unparalleled Data Quality
- Higher Quality Content
- 60% Fewer Hallucinations
Browse by: Latest US Patents, China's latest patents, Technical Efficacy Thesaurus, Application Domain, Technology Topic, Popular Technical Reports.
© 2025 PatSnap. All rights reserved.Legal|Privacy policy|Modern Slavery Act Transparency Statement|Sitemap|About US| Contact US: help@patsnap.com