Coal fine preparation, blowing method and device from packed-bed smelting reduction furnace
A coal powder preparation and reduction furnace technology, which is applied in the field of smelting reduction ironmaking, can solve the problems of large investment scale and large pollution, and achieve the effects of reducing coal cost, reducing production cost, and huge economic and social benefits
- Summary
- Abstract
- Description
- Claims
- Application Information
AI Technical Summary
Problems solved by technology
Method used
Image
Examples
Embodiment Construction
[0053] The embodiments are described below in conjunction with the accompanying drawings.
[0054] Referring to Figure 1, the raw coal suitable for COREX melting gasifier to produce reducing gas is crushed, screened and transported, and the crushed coal with a particle size below 5mm is loaded into the raw coal bunker 1 and supplied to the coal mill through the quantitative coal feeder 2 Coal mill 3 and coal mill 3 are fed with dry mixed gas for drying coal powder; coal powder is sucked into bag-type powder collector 7 by draft negative pressure after being dried and ground in coal mill 3, and in the bag-type powder collector 7 for gas-powder separation, and the filtered gas is sucked away from the top of the bag-type powder collector 7 by the exhaust fan 6 and discharged into the atmosphere through the chimney. collar storage.
[0055] The dry mixed gas fed into the coal mill is formed by mixing the high-temperature dry gas produced by the dry gas heating furnace 4 and the t...
PUM
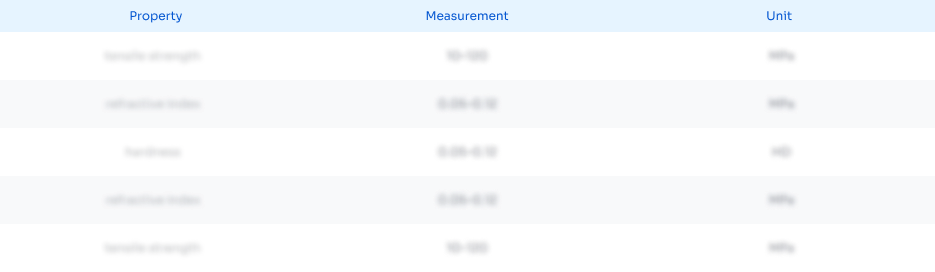
Abstract
Description
Claims
Application Information

- R&D
- Intellectual Property
- Life Sciences
- Materials
- Tech Scout
- Unparalleled Data Quality
- Higher Quality Content
- 60% Fewer Hallucinations
Browse by: Latest US Patents, China's latest patents, Technical Efficacy Thesaurus, Application Domain, Technology Topic, Popular Technical Reports.
© 2025 PatSnap. All rights reserved.Legal|Privacy policy|Modern Slavery Act Transparency Statement|Sitemap|About US| Contact US: help@patsnap.com