Semi-solid forming mold and method of use
A semi-solid forming and semi-solid slurry technology, which is applied in the field of non-ferrous metal preparation and processing, can solve the problems such as the decrease of the surface accuracy of the sizing belt, the coarse grain ring of the extruded material, and the boring car, and achieves a short processing process and is suitable for Wide range of effects with low energy consumption
- Summary
- Abstract
- Description
- Claims
- Application Information
AI Technical Summary
Problems solved by technology
Method used
Image
Examples
Embodiment 1
[0023] Example 1: Preparation of φ20mm magnesium alloy AZ91 bar
[0024] According to the φ20mm magnesium alloy to be prepared, the diameter of the outlet end of the cavity of the sizing die is selected to be 20 mm, and the taper of the sizing band of the sizing die is 1°. First, preheat the mold body and mold base of the mold to 575°C; the cooling chamber is cooled by circulating water, and the temperature of the circulating water is room temperature. After the AZ91 alloy is melted, the twin-screw mechanical stirring method is used to make semi-solid slurry. The temperature of the semi-solid slurry is 570°C. The feed temperature was also 570°C. Adjust the pore size of the flow valve to control the flow rate of the slurry to 0.2kg / s. The slurry enters the sizing die through the splitter cone to solidify to form a φ20mm rod.
Embodiment 2
[0025] Example 2: Prepare an aluminum alloy A356 pipe with an outer diameter of φ30mm and an inner diameter of φ25mm.
[0026] According to the aluminum alloy to be prepared with an outer diameter of φ30mm and an inner diameter of φ25mm, the diameter of the outlet end of the cavity of the sizing die is selected to be 30mm, the taper of the sizing band of the sizing die is 1°, and a mandrel of φ25mm is installed at one end of the mold splitter cone. Preheat the mold body and mold base of the mold to 608°C; the cooling chamber is cooled by circulating water, and the temperature of the circulating water is room temperature. After melting the A356 alloy, the electromagnetic stirring method was used to obtain a semi-solid slurry, and the temperature of the semi-solid slurry was 605°C. The semi-solid slurry enters the mold under the action of the piston-type pushing device, and the temperature of the semi-solid slurry at the outlet of the piston-type pushing device is also 605°C. A...
PUM
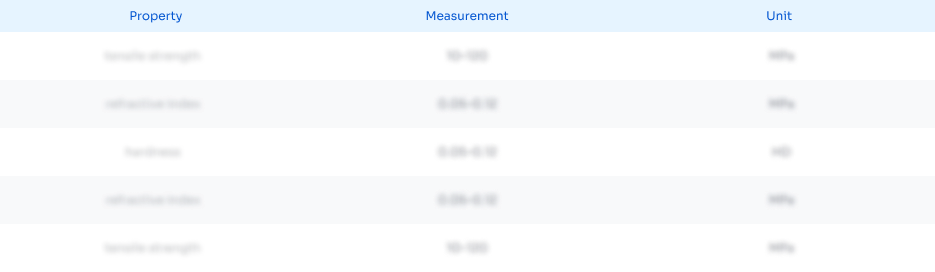
Abstract
Description
Claims
Application Information

- Generate Ideas
- Intellectual Property
- Life Sciences
- Materials
- Tech Scout
- Unparalleled Data Quality
- Higher Quality Content
- 60% Fewer Hallucinations
Browse by: Latest US Patents, China's latest patents, Technical Efficacy Thesaurus, Application Domain, Technology Topic, Popular Technical Reports.
© 2025 PatSnap. All rights reserved.Legal|Privacy policy|Modern Slavery Act Transparency Statement|Sitemap|About US| Contact US: help@patsnap.com