Force compensation method for keying head of full-automatic wire keying machine
A wire bonding machine and wire bonding technology, applied in semiconductor devices, electrical components, circuits, etc., can solve the problem of contact detection failure between the bonding head and the chip surface, large impact between the bonding head and the chip surface, and reduce dynamics characteristics and other problems, to solve the problem of detection failure, improve the consistency of arc and welding quality, and suppress the impact force
- Summary
- Abstract
- Description
- Claims
- Application Information
AI Technical Summary
Problems solved by technology
Method used
Image
Examples
Embodiment Construction
[0022] Such as figure 1 As shown, the motion control system of the automatic wire bonding machine is composed of the host, motion controller, servo amplifier, grating scale feedback element, bonding head linear motor and actuator, pressure sensor and other parts. Based on the force / position hybrid control algorithm, the main engine and the motion controller respectively realize the position closed-loop and force / acceleration closed-loop control of the linear motor of the bonding head and the actuator through the grating ruler and the pressure sensor.
[0023] When adjusting the motion parameters of each servo axis motor of the fully automatic bonding machine, the host reads the status of the slave from the data exchange memory of the motion controller DSP, judges whether all previous motion commands are completed, and MotionDone() runs in a loop until until the exercise is complete. The servo calculation cycle in the DSP of the motion controller first calls the encoder readi...
PUM
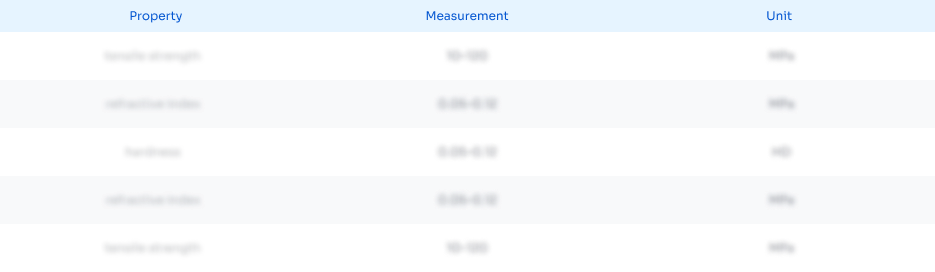
Abstract
Description
Claims
Application Information

- Generate Ideas
- Intellectual Property
- Life Sciences
- Materials
- Tech Scout
- Unparalleled Data Quality
- Higher Quality Content
- 60% Fewer Hallucinations
Browse by: Latest US Patents, China's latest patents, Technical Efficacy Thesaurus, Application Domain, Technology Topic, Popular Technical Reports.
© 2025 PatSnap. All rights reserved.Legal|Privacy policy|Modern Slavery Act Transparency Statement|Sitemap|About US| Contact US: help@patsnap.com