Energy-saving shape cutting method of composite floor
A composite floor, profiling and cutting technology, applied in the direction of floors, building structures, wood processing appliances, etc., can solve the problems of difficult installation of finished wood floors, affecting quality, and easy operation errors.
- Summary
- Abstract
- Description
- Claims
- Application Information
AI Technical Summary
Problems solved by technology
Method used
Image
Examples
Embodiment Construction
[0013] The composite floor substrate cutting method of the present invention is divided into primary and secondary slotting profiling cutting methods.
[0014] The specific implementation steps of the method of secondary slotting:
[0015] 1. Select the upper slotting tool 6 and the lower slotting tool 7: according to the upper and lower locking structures A and B of the finished wooden floor 5, select the upper slotting tool 6 and the lower slotting tool 7, and the upper slotting tool 6 and The lower grooving tool 7 can be a common flat saw blade or a profiling saw blade close to the shape of the forming lock;
[0016] 2. According to the structure A, B of the finished wooden floor 5 lock and the upper slotting tool 6 and the lower slotting tool 7, determine the cutting depth of the upper slot 2 and the lower slot 3, and determine the distance between the upper slot 2 and the lower slot 3 the width of the connecting portion 4;
[0017] 3. Determine the cutting position of t...
PUM
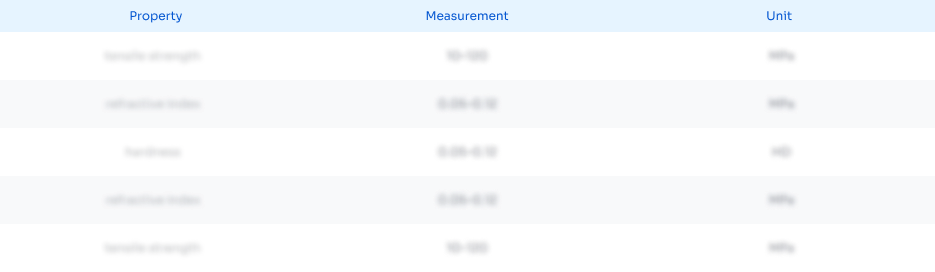
Abstract
Description
Claims
Application Information

- R&D
- Intellectual Property
- Life Sciences
- Materials
- Tech Scout
- Unparalleled Data Quality
- Higher Quality Content
- 60% Fewer Hallucinations
Browse by: Latest US Patents, China's latest patents, Technical Efficacy Thesaurus, Application Domain, Technology Topic, Popular Technical Reports.
© 2025 PatSnap. All rights reserved.Legal|Privacy policy|Modern Slavery Act Transparency Statement|Sitemap|About US| Contact US: help@patsnap.com