Manganese zinc ferrite of high magnetic conductivity high saturation magnetic flux density high Curie temperature
A technology of ferrite material and magnetic flux density, applied in the field of MnZn ferrite, which can solve the problems of reducing volume and narrow installation space.
- Summary
- Abstract
- Description
- Claims
- Application Information
AI Technical Summary
Problems solved by technology
Method used
Image
Examples
preparation example Construction
[0018] A typical embodiment of the ferrite preparation method of the present invention, with the following steps:
[0019]1) Mixing of raw materials: According to the following raw material formula: Fe 2 o 3 : 54.1mol%, ZnO: 13mol%, MnO: 32.9mol% Weigh raw materials;
[0020] 2) Sanding once:
[0021] Put the weighed raw materials into the sand mill, and add equal weight of deionized water in advance, and sand for 0.5 hours;
[0022] 3) Primary spray drying granulation:
[0023] Add about 10% PVA solution (concentration is 10%) in raw material slurry, carry out spray drying granulation once;
[0024] 4) Pre-burning: the primary spray-dried granulated powder is pre-fired through a rotary kiln, and the firing temperature is 900°C;
[0025] 5) Addition of impurities (ingredients): Add the following auxiliary components: CoO: 0.08wt%, Bi 2 o 3 : 0.03wt%; while MoO 3 : 0.02wt%, CaO: 0.045wt%, In 2 o 3 : 0.035wt% and WO 3 : 0.02wt% four kinds of added ingredients can be a...
Embodiment 1
[0031] Embodiment 1: take by weighing 54.1mol% Fe 2 o 3 , 32.9mol% MnO (raw material form is Mn3O4), 13mol% ZnO. Put it into a sand mill pre-added with deionized water to grind, control the average particle size to 0.8±0.2μm, and pre-fire it with an electric rotary kiln at a temperature of 900±20°C after one spray. Then the pre-fired material is put into a sand mill for secondary sand grinding. During the sand grinding process, 35% of pure water, 0.008% of dispersant and 0.005% of defoamer are added relative to the content of the main component, and the additive CaO: 0.045wt% is added. 、WO 3 : 0.02wt%, CoO: 0.08wt%, Bi 2 o 3 : 0.03wt% to control the average particle size of the sand mill to be 1.0±0.2μm. Finally, secondary spraying is carried out to obtain MnZn ferrite particle powder. Take the pellets and press them into φ25mm×φ15mm×7.5mm, the density is about 3.0±0.2g / cm 3 Put the ferrite blank into a bell furnace, and sinter at 1395°C for 5 hours in an equilibrium at...
Embodiment 2
[0032] Embodiment 2: take by weighing 53.5mol% Fe 2 o 3 , 34.5mol% MnO (raw material form is Mn 3 o 4 ), 12mol% ZnO. Put it into a sand mill pre-added with deionized water to grind, control the average particle size to 0.8±0.2μm, and pre-fire it with an electric rotary kiln at a temperature of 900±20°C after one spray. Then the pre-fired material is put into a sand mill for secondary sand grinding. During the sand grinding process, 35% of pure water, 0.008% of dispersant and 0.005% of defoamer are added relative to the content of the main component, and the additive CaO: 0.045wt% is added. 、In 2 o 3 : 0.035wt%, WO 3 : 0.02wt%, CoO: 0.08wt%, Bi 2 o 3 : 0.03wt%, MoO 3 : 0.02wt%, the average grain size of the controlled sand mill is 1.0±0.2μm. Finally, secondary spraying is carried out to obtain Mn-Zn ferrite particle powder. Take the pellets and press them into φ25mm×φ15mm×7.5mm, the density is about 3.0±0.2g / cm 3 Put the ferrite blank into a bell furnace, and sinter...
PUM
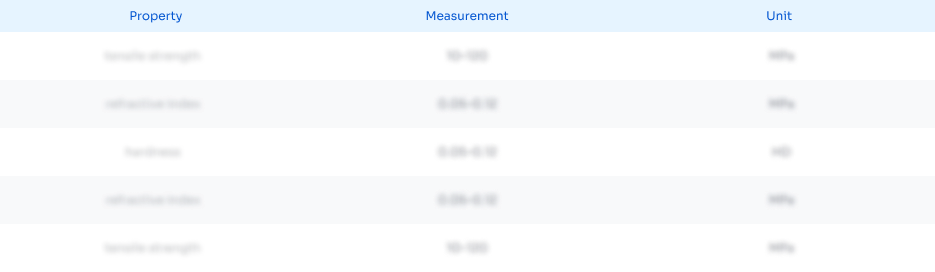
Abstract
Description
Claims
Application Information

- R&D Engineer
- R&D Manager
- IP Professional
- Industry Leading Data Capabilities
- Powerful AI technology
- Patent DNA Extraction
Browse by: Latest US Patents, China's latest patents, Technical Efficacy Thesaurus, Application Domain, Technology Topic, Popular Technical Reports.
© 2024 PatSnap. All rights reserved.Legal|Privacy policy|Modern Slavery Act Transparency Statement|Sitemap|About US| Contact US: help@patsnap.com