Polyester type amphipathic nature ultra-dispersant and preparation method thereof
A hyperdispersant and amphiphilic technology, applied in chemical instruments and methods, transportation and packaging, dissolution, etc., can solve problems such as inappropriateness, achieve short production cycle, good amphiphilic performance, and popularize the use of the effect
- Summary
- Abstract
- Description
- Claims
- Application Information
AI Technical Summary
Problems solved by technology
Method used
Image
Examples
Embodiment approach 1
[0033] In Embodiment 1, 19.1879 g of ethyl acrylate, 12.0068 g of methyl methacrylate, 11.9445 g of methacrylic acid and 2.8782 g of ethylenediamine were weighed respectively. Corresponding to a molar ratio of 4:2.5:2.86:1, add 92g of distilled water into a 250mL four-necked reaction flask, and heat in a water bath. When the temperature rose to 80°C, 1.1504 g of KPS were added. Start stirring, and when KPS is completely dissolved, add ethyl acrylate and methyl methacrylate mixed monomers dropwise with a constant pressure dropper. After adding the mixed monomer, start to add methacrylic acid dropwise after 2 hours of constant temperature reaction, start to add ethylenediamine dropwise after the methacrylic acid is added and keep the constant temperature reaction for 2 hours, after the addition of ethylenediamine is completed, continue to react for 4 hours, and then stop the reaction . The obtained product is separated into liquids, and the oily liquid in the upper layer is th...
Embodiment approach 2
[0034] In Embodiment 2, 19.1879 g of ethyl acrylate, 12.0068 g of methyl methacrylate, 11.9445 g of methacrylic acid and 2.8782 g of ethylenediamine were weighed respectively. Corresponding to a molar ratio of 4:2.5:2.86:1, add 80g of distilled water into a 250mL four-neck reaction flask and heat it with a water bath. When the temperature rose to 50°C, 1.8410 g KPS was added. Start stirring, when KPS is completely dissolved, add ethyl acrylate, methyl methacrylate mixed monomer and 8g of 0.7mol / L sodium bisulfite solution to the reaction bottle at the same time, after the materials are added, react at constant temperature for 2h, and then At the same time, methacrylic acid and 4 g of 0.7 mol / L sodium bisulfite solution were added dropwise, and the reaction was continued for 2 hours after the addition of the materials, and then ethylenediamine was added dropwise. After the addition of ethylenediamine, the reaction was continued at constant temperature for 3 hours, and then the...
Embodiment approach 3
[0035] In Embodiment 3, 19.1879 g of ethyl acrylate, 12.0068 g of methyl methacrylate, 8.2437 g of acrylic acid and 2.8782 g of ethylenediamine were weighed respectively. Corresponding to a molar ratio of 4:2.5:2.86:1, add 92g of distilled water into a 250mL four-necked four-necked reaction flask and heat it with a water bath. When the temperature rose to 80°C, 1.1504 g of KPS were added. Start stirring, and when KPS is completely dissolved, add ethyl acrylate and methyl methacrylate mixed monomers dropwise with a constant pressure dropper. After adding the mixed monomers, start to add acrylic acid dropwise after the constant temperature reaction for 2 hours, start to add ethylenediamine dropwise after the addition of acrylic acid and keep the constant temperature reaction for 2 hours, and continue the reaction for 4 hours after the addition of ethylenediamine, and then stop the reaction. The obtained product is liquid-separated, and the oily liquid in the upper layer is the ...
PUM
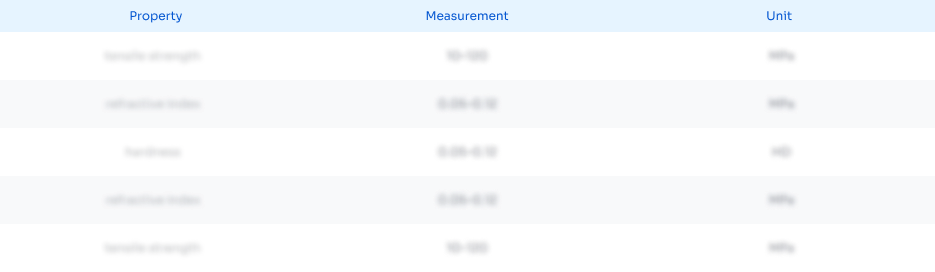
Abstract
Description
Claims
Application Information

- R&D
- Intellectual Property
- Life Sciences
- Materials
- Tech Scout
- Unparalleled Data Quality
- Higher Quality Content
- 60% Fewer Hallucinations
Browse by: Latest US Patents, China's latest patents, Technical Efficacy Thesaurus, Application Domain, Technology Topic, Popular Technical Reports.
© 2025 PatSnap. All rights reserved.Legal|Privacy policy|Modern Slavery Act Transparency Statement|Sitemap|About US| Contact US: help@patsnap.com