Industrial robot cutting and processing system applied to auxiliary assembly of airplane as well as method
An industrial robot and cutting processing technology, applied in the direction of metal processing equipment, metal processing machinery parts, positioning devices, etc., can solve problems such as single function, no technical reports, and inability to meet processing accuracy requirements
- Summary
- Abstract
- Description
- Claims
- Application Information
AI Technical Summary
Problems solved by technology
Method used
Image
Examples
Embodiment Construction
[0023] Embodiments of the present invention will be described in detail below in conjunction with the accompanying drawings. The industrial robot cutting processing system of this embodiment is realized according to the foregoing scheme.
[0024] Such as figure 1 As shown, the industrial robot cutting processing system applied to aircraft auxiliary assembly includes an industrial robot cutting processing device and a laser tracker 8, and the industrial robot cutting processing device includes an operation panel 1, a robot controller 2, a six-axis articulated serial industrial robot 3, Target mounting flange 4, tool quick changer 5, tool clamping fixture 6, high-speed electric spindle 7, six-axis articulated series industrial robot 3 ends are provided with target mounting flange 4, tool quick changer 5, tool clamping in turn Tooling 6, high-speed electric spindle 7.
[0025] The six-axis articulated serial industrial robot 3 is an ABB IRB6600 industrial robot, which is driven...
PUM
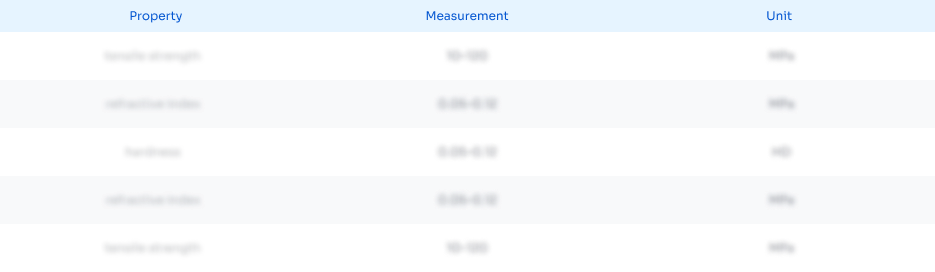
Abstract
Description
Claims
Application Information

- R&D
- Intellectual Property
- Life Sciences
- Materials
- Tech Scout
- Unparalleled Data Quality
- Higher Quality Content
- 60% Fewer Hallucinations
Browse by: Latest US Patents, China's latest patents, Technical Efficacy Thesaurus, Application Domain, Technology Topic, Popular Technical Reports.
© 2025 PatSnap. All rights reserved.Legal|Privacy policy|Modern Slavery Act Transparency Statement|Sitemap|About US| Contact US: help@patsnap.com