Austenite ductile iron with low nickle content and high manganses and chromium content and technology thereof
A technology of ductile cast iron and process method, which is applied in the field of low-nickel, high-manganese, high-chromium austenitic ductile iron and its process, which can solve problems such as easy rust, high alloy hardness, and difficult cutting, so as to save consumption and have strong deoxidation ability , the effect of improving performance
- Summary
- Abstract
- Description
- Claims
- Application Information
AI Technical Summary
Problems solved by technology
Method used
Image
Examples
Embodiment 1
[0023] The invention relates to the melting of low-nickel, high-manganese and high-chromium austenitic nodular cast iron. The proportion by weight of each component is: C 1.0%, Si 2%, Mn 11%, Ni 2.5%, Cr 14.5%, Cu 2.7%, and the rest is Fe. Furnace materials include ordinary pig iron, scrap steel (shavings), recycled materials, low-carbon ferromanganese, electrolytic nickel, ferrochrome, electrolytic copper, and 75 ferrosilicon. Iron and 0.6% calcium silicon, stir evenly, pour standard bending test rods and cylindrical castings with precision type 55 (outer diameter) X20 (inner diameter) X85 (height) mm, cool to below 600 ℃ and drop wax to seal sand, cool , as-cast metallographic microstructure see figure 1 , composed of fine A-type graphite flakes, austenite matrix and fine granular carbides, the number of carbides is 1.2%. The fracture of the casting is thin, dense, free of inclusions and non-magnetic.
[0024] Table 1 lists the alloy mechanical properties and austenite th...
Embodiment 2
[0028] The invention relates to the melting of low-nickel, high-manganese and high-chromium austenitic nodular cast iron. The proportion by weight of each component is: C 1.0%, Si 2.2%, Mn 12.5%, Ni 3.8%, Cu 2.0%, Cr 14.5%. Furnace materials include ordinary pig iron, scrap steel (shavings), recycled materials, low-carbon ferromanganese, electrolytic nickel, ferrochrome, electrolytic copper, and 75 ferrosilicon. Ferrosilicon, and then rush into 0.7% calcium silicon with the molten iron flow for instantaneous inoculation. Use precision pouring standard bending test rods and cylindrical castings 55 (outer diameter) X 20 (inner diameter) X 85 (height) mm. Cool to below 600°C to shake out sand and air cool. The fracture of the casting is thin, dense, free of inclusions and non-magnetic. As-cast metallographic structure (see figure 2 ) consists of fine curved A-type graphite flakes, an austenite matrix and fine granular carbides. The amount of carbides is less than 1.2%, even...
PUM
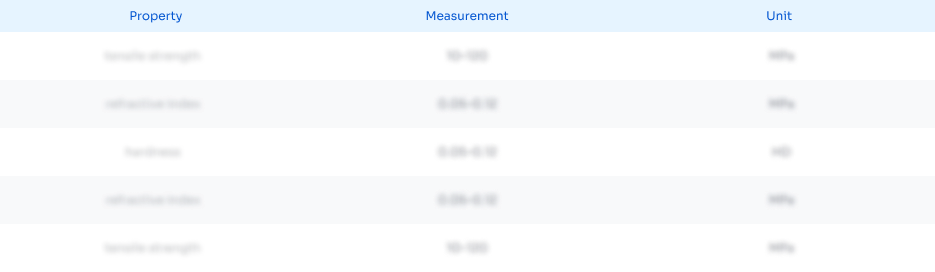
Abstract
Description
Claims
Application Information

- R&D Engineer
- R&D Manager
- IP Professional
- Industry Leading Data Capabilities
- Powerful AI technology
- Patent DNA Extraction
Browse by: Latest US Patents, China's latest patents, Technical Efficacy Thesaurus, Application Domain, Technology Topic, Popular Technical Reports.
© 2024 PatSnap. All rights reserved.Legal|Privacy policy|Modern Slavery Act Transparency Statement|Sitemap|About US| Contact US: help@patsnap.com