Casting machine head capable of adjusting pipe accessory temperature with different material constituents
An adjustable, raw material technology, applied in the field of pouring machine head, can solve the problems of shortening the service life of equipment, high manufacturing and maintenance costs, and high melting point
- Summary
- Abstract
- Description
- Claims
- Application Information
AI Technical Summary
Problems solved by technology
Method used
Image
Examples
Embodiment 1
[0032] Embodiment 1: a low-temperature raw material chamber and a high-temperature raw material chamber are arranged in the body.
[0033] The present invention comprises a body 6, a raw material mixing chamber 1 and a machine head heat conduction oil circulation circuit 26. A stirrer 31 equipped with a mixing chamber stirring drive motor 15 is placed in the raw material mixing chamber 1. In the body 6, there are The low-temperature raw material chamber 5, the intermediate feed chamber 16 and the high-temperature raw material chamber 25 are provided with a low-temperature raw material pouring circulation switching valve 10 and a low-temperature raw material pipeline pressure regulating valve 4 in the low-temperature raw material chamber 5, and a high-temperature raw material chamber 25 is provided with a high-temperature Raw material pouring cycle switching valve 20 and high temperature raw material pipeline pressure regulating valve 21, machine head heat transfer oil circulati...
Embodiment 2
[0043] Embodiment 2: Two low-temperature raw material chambers and two high-temperature raw material chambers are arranged in the body, and the heat-conducting medium in the high-temperature raw material feed pipe where one high-temperature raw material component is located and the heating insulation jacket of the high-temperature raw material return pipe are removed and supplied. In addition to the heating and heat preservation of the high-temperature raw material room and the intermediate feeding room where it is located, it also provides heating and heat preservation for two low-temperature raw material rooms.
[0044]The present invention includes a machine body 6, a raw material mixing chamber 1, a first machine head heat transfer oil circulation circuit 26, and a second machine head heat transfer oil circulation circuit 50, and a stirrer 31 equipped with a mixing chamber stirring drive motor 15 is placed in the raw material mixing chamber 1 , the body is provided with the...
Embodiment 3
[0058] Embodiment 3: Two low-temperature raw material chambers and two high-temperature raw material chambers are arranged in the body, and the heat-conducting medium in the high-temperature raw material feed pipe where one high-temperature raw material component is located and the heating insulation jacket of the high-temperature raw material return pipe are removed and supplied. In addition to heating and insulating the high-temperature raw material room and the intermediate feeding room where it is located, it also provides heating and heat preservation for a low-temperature raw material room; the other high-temperature raw material component is located in the heating and insulating jacket of the high-temperature raw material feeding pipe and the high-temperature raw material return pipe In addition to heating and insulating the high-temperature raw material room where it is located, the heat-conducting medium also provides heating and heat preservation for a low-temperature ...
PUM
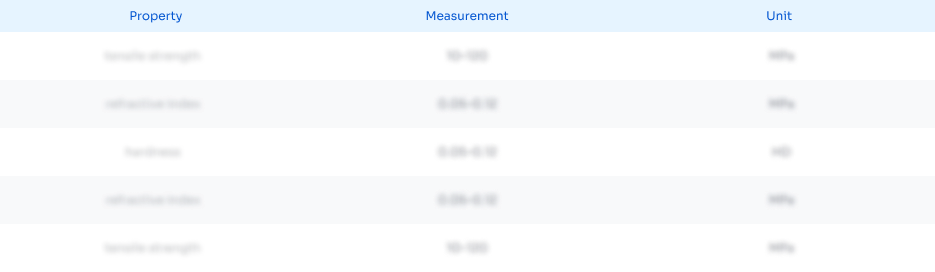
Abstract
Description
Claims
Application Information

- R&D
- Intellectual Property
- Life Sciences
- Materials
- Tech Scout
- Unparalleled Data Quality
- Higher Quality Content
- 60% Fewer Hallucinations
Browse by: Latest US Patents, China's latest patents, Technical Efficacy Thesaurus, Application Domain, Technology Topic, Popular Technical Reports.
© 2025 PatSnap. All rights reserved.Legal|Privacy policy|Modern Slavery Act Transparency Statement|Sitemap|About US| Contact US: help@patsnap.com