Sifting and manufacturing method for macromolecule lens
A polymer and lens technology, which is applied in the field of polymer lens sieve method, can solve problems such as unstable work efficiency, unpredictable actual times of mold repairs, and impact of mold repair times on cost and delivery time, etc.
- Summary
- Abstract
- Description
- Claims
- Application Information
AI Technical Summary
Problems solved by technology
Method used
Examples
Embodiment 1
[0029] This example illustrates the process of screening a biconvex spherical lens with the method of the present invention.
[0030] Design a symmetrical biconvex spherical lens with a focal length of 1.00±0.01 cm. Select the polymer material whose refractive index n is 1.5, then according to the mirror maker's formula of biconvex spherical lens, the radius of the required spherical surface (R 1 = R 2) is 1 cm. Because the required focal length error is within 0.01 cm, it is possible to use a spherical equation with a radius of about 1 cm and change every 0.01 cm to make the cavity of the pre-mold. Therefore, using the previous mold with 20 mold cavities, the radii of the spherical equations are 0.90, 0.91, 0.92, ..., 1.07, 1.08, 1.09 cm to screen the required polymer lens. After processing by injection molding, a lens with a focal length of 1.00±0.005 cm can be screened out. Then according to the spherical equation of the mold cavity screened out, a production mold with ...
Embodiment 2
[0032] This example illustrates the process of sieving an aspheric lens with the method of the present invention.
[0033] Design an aspherical lens with a focal length of 10.0±0.2 cm and low aberration (the maximum focal length difference is less than 0.2 cm). A polymer material with a refractive index n of 1.5 is selected. A radius of 30 centimeters spherical equation (adjustable focal length) and a paraboloid equation y=12(x 2 +y 2 ) Overlapping lens bodies can meet the needs. For a lens with a diameter of 1 cm, with the paraboloid equation y=12(x 2 +y 2 ) is mainly used for aberration focus correction, and y=12(x 2 +y 2 )+c(x 2 +y 2 ) 2 The surface equation is used to make the mold cavity of the previous mold. Because the required aberration focal length error is within 0.2 centimeters, it is desirable to change c every 0.2 centimeters. Using the previous mold with 25 mold cavities, c is -0.4, -0.2, 0, 0.2 and 0.4. And match the spherical equation with radius o...
Embodiment 3
[0035] This embodiment illustrates the process of screening spherical lenses with low chromatic aberration by the method of the present invention.
[0036] Design a group of spherical lens groups with an equivalent focal length of 10.0±0.2 centimeters and a difference of equivalent focal lengths between blue light and red light within 0.2 centimeters. Select polycarbonate (PC) with a refractive index n of 1.58 and an Abbe number A of 58, and an acrylic resin (PMMA) with a refractive index n of 1.49 and an Abbe number A of 30 as materials for compensating for chromatic aberration. Let the focal lengths of the lenses formed by PC and PMMA be f 1 and f 2 , then the equivalent focal length f of the spherical lens group E It can be determined by the following formula:
[0037] 1 / f E =1 / f 1 +1 / f 2 =1 / 10
[0038] while f 1 A 1 +f 2 A 2 =0=58A 1 +30A 2
[0039] Solving the simultaneous equations gives f 1 = 280 / 58 = 4.83, f 2 =-28 / 3=-9.33. Therefore, the required lens...
PUM
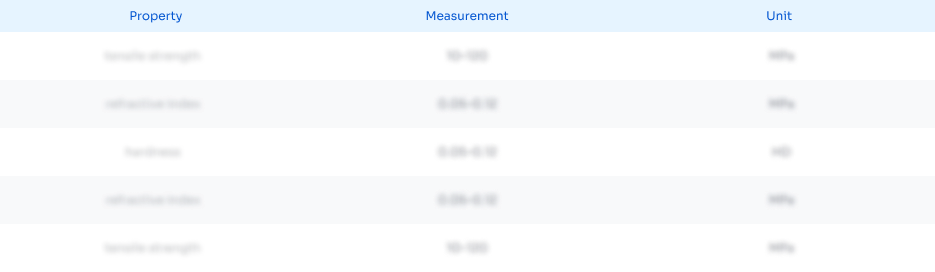
Abstract
Description
Claims
Application Information

- R&D
- Intellectual Property
- Life Sciences
- Materials
- Tech Scout
- Unparalleled Data Quality
- Higher Quality Content
- 60% Fewer Hallucinations
Browse by: Latest US Patents, China's latest patents, Technical Efficacy Thesaurus, Application Domain, Technology Topic, Popular Technical Reports.
© 2025 PatSnap. All rights reserved.Legal|Privacy policy|Modern Slavery Act Transparency Statement|Sitemap|About US| Contact US: help@patsnap.com