Preparation method for magnesium alloy cast paint
A technology for casting coatings and magnesium alloys, applied in casting molding equipment, metal processing equipment, coatings, etc., can solve problems such as hot cracking of magnesium castings, and achieve the effects of preventing oxidation, smooth surface, and excellent suspension.
- Summary
- Abstract
- Description
- Claims
- Application Information
AI Technical Summary
Problems solved by technology
Method used
Examples
Embodiment
[0006] Embodiment: a kind of preparation method of magnesium alloy casting paint, 0.7% palygorskite clay is mixed with 17% water and grinds for 3 hours, makes first liquid, then 5% talcum powder, 3% diatomite, 0.5% Put KBF4 and 1% aluminum phosphate into the ball mill, add solution A, 3% silica sol and 67.6% water and grind for 3 hours to get magnesium alloy metal mold casting coating, heat the metal mold to about 200°C and spray it on the metal mold The surface is coated with a layer of magnesium alloy casting paint, and it can be dried after drying.
PUM
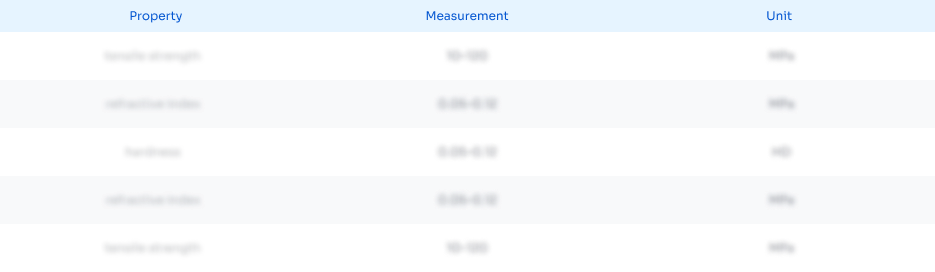
Abstract
Description
Claims
Application Information

- R&D
- Intellectual Property
- Life Sciences
- Materials
- Tech Scout
- Unparalleled Data Quality
- Higher Quality Content
- 60% Fewer Hallucinations
Browse by: Latest US Patents, China's latest patents, Technical Efficacy Thesaurus, Application Domain, Technology Topic, Popular Technical Reports.
© 2025 PatSnap. All rights reserved.Legal|Privacy policy|Modern Slavery Act Transparency Statement|Sitemap|About US| Contact US: help@patsnap.com