Sodion compensating potassium and sodium niobate based leadless piezoelectric ceramics and method for preparing same
A potassium-sodium niobate-based, lead-free piezoelectric technology, applied in piezoelectric/electrostrictive/magnetostrictive devices, circuits, electrical components, etc., can solve the problem of lowering the sintering temperature, high lead-free piezoelectric ceramics, and See and other problems, to achieve the effect of reducing the sintering temperature
- Summary
- Abstract
- Description
- Claims
- Application Information
AI Technical Summary
Problems solved by technology
Method used
Image
Examples
Embodiment 1
[0021] According to (Na 0.211+0.001 K 0.77 Li 0.019 )NbO 3 (x=0.001) formula, weigh 0.389gNa respectively with electronic balance 2 CO 3 , 1.812gK 2 CO 3 , 0.024gLi 2 CO 3 , and 4.533gNb 2 o 5 , using absolute ethanol as the medium, grinding and mixing the materials with a planetary ball mill for 24 hours at a speed of 250 rpm, and drying the slurry at 80° C. to obtain dry powder. The dry powder was subjected to 700°C and kept for 10 hours to synthesize niobate. Take 0.3g of powder and put it into a Φ10mm mold, and press it into shape. The formed discs were sintered in a programmed temperature-controlled box furnace, sintered at 1000° C., kept for 2 hours, and cooled to room temperature to obtain ceramic discs. After grinding with 600-mesh fine sandpaper, coat both surfaces with baked silver electrodes to make baked silver ceramic sheets, put them in silicone oil and heat to 100°C, keep at 5kV / mm voltage for 20min for polarization, and then cool down to room temper...
Embodiment 2
[0023] According to (Na 0.732+0.20 K 0.204 Li 0.064 )NbO 3 (x=0.20) formula, weigh 0.84gNa respectively with electronic balance 2 O, 0.507gK 2 CO 3 , 0.085gLi 2 CO 3 , and 4.786gNb 2 o 5 , using absolute ethanol as the medium, grinding and mixing the materials with a planetary ball mill for 3 hours at a rotation speed of 250 rpm, and drying the slurry at 80° C. to obtain dry powder. The dry powder was subjected to 750°C and kept for 7 hours to synthesize niobate. Take 0.3g of powder and put it into a Φ10mm mold, and press it into shape. The formed discs were sintered in a programmed temperature-controlled box furnace, sintered at 800° C., kept for 5 hours, and cooled to room temperature to obtain ceramic discs. After grinding with 600-mesh fine sandpaper, apply baked silver electrodes on both surfaces to make baked silver ceramic sheets, put them in silicone oil and heat to 200°C, keep at 5kV / mm voltage for 30min for polarization, and then cool down to room temperat...
Embodiment 3
[0025] According to (Na 0.516+0.01- K 0.446 Li 0.038 )NbO 3 (x=0.01) formula, weigh 1.553gNaHCO respectively with electronic balance 3 , 1.082gK 2 CO 3 , 0.049gLi 2 CO 3 , and 4.673gNb 2 o 5 , using absolute ethanol as the medium, grinding and mixing the materials with a planetary ball mill for 12 hours at a speed of 250 rpm, and drying the slurry at 80° C. to obtain dry powder. The dry powder was subjected to 850°C and kept for 5 hours to synthesize niobate. Take the powder for 0.3h, put it into a Φ10mm mold, and press to form it. The formed discs were sintered in a programmed temperature-controlled box furnace, sintered at 940° C., kept for 4 hours, and cooled to room temperature to obtain ceramic discs. After grinding with 600-mesh fine sandpaper, coat both surfaces with baked silver electrodes to make baked silver ceramic sheets, heat them in silicone oil to 140°C, keep at 4kV / mm voltage for 50min for polarization, and then cool down to room temperature to compl...
PUM
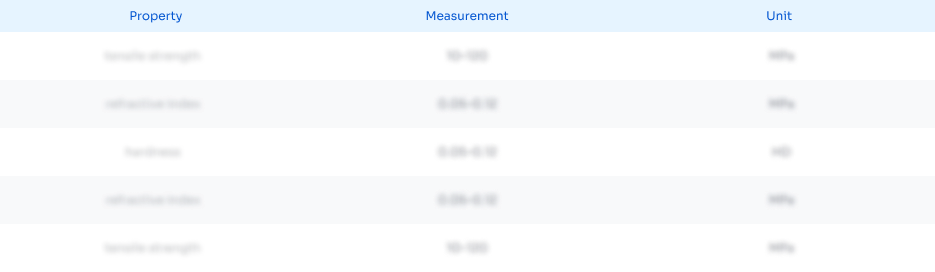
Abstract
Description
Claims
Application Information

- R&D
- Intellectual Property
- Life Sciences
- Materials
- Tech Scout
- Unparalleled Data Quality
- Higher Quality Content
- 60% Fewer Hallucinations
Browse by: Latest US Patents, China's latest patents, Technical Efficacy Thesaurus, Application Domain, Technology Topic, Popular Technical Reports.
© 2025 PatSnap. All rights reserved.Legal|Privacy policy|Modern Slavery Act Transparency Statement|Sitemap|About US| Contact US: help@patsnap.com