Method for rolling and shaping stainless steel special-shaped ring forging
A special-shaped ring and stainless steel technology, applied in the direction of metal rolling, etc., can solve problems such as unfavorable equipment maintenance, inaccurate selection of deformation, folding, etc., to facilitate maintenance of equipment, reduce machining allowance, and reduce manufacturing costs. cost effect
- Summary
- Abstract
- Description
- Claims
- Application Information
AI Technical Summary
Problems solved by technology
Method used
Image
Examples
specific Embodiment approach
[0029] The content of the main chemical elements (percentage by weight) of the alloy is: 0.06% to 0.11% of C, 9.80% to 11.20% of Cr, 5.0% to 7.0% of Co, 0.10% to 0.70% of Si, 0.10% to 0.70% of Si, Mo content 0.50%~1.0%, Mn content 0.60%~1.15%, Nb content 0.05%~0.15%, V content 0.10%~0.35%, Ni content 0.20%~0.80%, N content 0.010%~ 0.035%, B content 0.004% ~ 0.012%, P content ≤ 0.028%, S content ≤ 0.02%, the balance is Fe.
[0030] The process steps of the alloy from the bar to the production of qualified special-shaped ring forgings are as follows:
[0031] Step 1: Billet making of a rectangular pre-rolled billet. Such as figure 1 As shown, the 10Cr-6Co-0.8Mo alloy bar 1 blanked according to the specification is heated to the deformation temperature of 1130 ° C ~ 1150 ° C in the forging heating furnace, and it is upset on the forging press to deform 50% ~ 55% to obtain a solid Round cake 2, then the solid round cake 2 is punched out of the central hole with a punch 4 to obt...
PUM
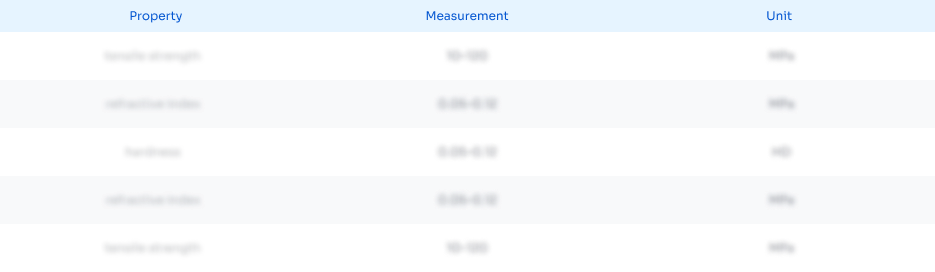
Abstract
Description
Claims
Application Information

- R&D
- Intellectual Property
- Life Sciences
- Materials
- Tech Scout
- Unparalleled Data Quality
- Higher Quality Content
- 60% Fewer Hallucinations
Browse by: Latest US Patents, China's latest patents, Technical Efficacy Thesaurus, Application Domain, Technology Topic, Popular Technical Reports.
© 2025 PatSnap. All rights reserved.Legal|Privacy policy|Modern Slavery Act Transparency Statement|Sitemap|About US| Contact US: help@patsnap.com