Microstructure appearance test method based on infrared white light interference technique
A technology of white light interference and testing method, which is applied to measurement devices, optical devices, instruments, etc., can solve the problem of inability to measure the sidewall topography of deep trench structures, and achieve the effect of wide application fields
- Summary
- Abstract
- Description
- Claims
- Application Information
AI Technical Summary
Problems solved by technology
Method used
Image
Examples
Embodiment Construction
[0016] The microstructure morphology testing method based on infrared white light interference technology is realized in the following steps:
[0017] 1), on the basis of not damaging the surface morphology of the sidewall to be tested in the deep groove structure of the device under test 1, a non-destructive treatment is performed on the sidewall to be tested to prevent infrared transmission;
[0018] 2), (such as figure 1 As shown) the infrared light source 2 is used as the measurement light source. The infrared light emitted by the infrared light source 2 is adjusted by the lens group 3 to become a parallel beam. The parallel beam is divided into a reference beam and a detection beam by the beam splitter 4. The detection beam penetrates the deep groove structure The side wall to be measured is coherently superimposed with the reference beam reflected by the reference mirror 5 after being reflected by the side wall and the non-destructively processed interface, forming a lig...
PUM
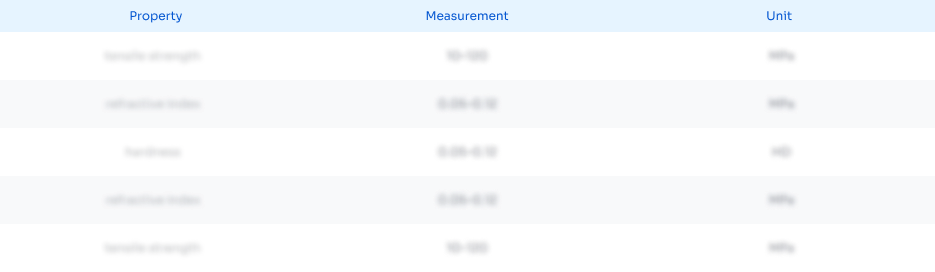
Abstract
Description
Claims
Application Information

- R&D
- Intellectual Property
- Life Sciences
- Materials
- Tech Scout
- Unparalleled Data Quality
- Higher Quality Content
- 60% Fewer Hallucinations
Browse by: Latest US Patents, China's latest patents, Technical Efficacy Thesaurus, Application Domain, Technology Topic, Popular Technical Reports.
© 2025 PatSnap. All rights reserved.Legal|Privacy policy|Modern Slavery Act Transparency Statement|Sitemap|About US| Contact US: help@patsnap.com