Cell-type car-type heating stove highly effective combustion system
A combustion system and heating furnace technology, applied in lighting and heating equipment, furnaces, furnace components, etc., can solve the problems of only about 40%, blockage of burners, long soaking time, etc., to reduce oxidation burning Loss rate, extended service life, high degree of automation effect
- Summary
- Abstract
- Description
- Claims
- Application Information
AI Technical Summary
Problems solved by technology
Method used
Image
Examples
Embodiment Construction
[0035] Below the present invention will be further described in conjunction with the embodiment in the accompanying drawing:
[0036] Figure 3~ Figure 7 Shown: including several pairs of regenerative left burners 1, left reversing valve 2, left gas quick cut valve 3, smoke main pipe 4, air main pipe 5, gas main pipe 6, right gas quick cut valve 7, Right reversing valve 8, regenerative right burner 9, combustion-supporting blower 10, hood 11.
[0037] Figure 3~ Figure 7 As shown, according to the charging characteristics of chamber-type and trolley-type heating furnaces, the present invention arranges several pairs of regenerative type left and right side burners on the two sides of the furnace roof that can avoid the flame scouring the billet as much as possible and obtain the largest combustion space. side. According to the requirements of different equipment levels of users, the present invention can adopt the "full decentralized" reversing control mode in which each set ...
PUM
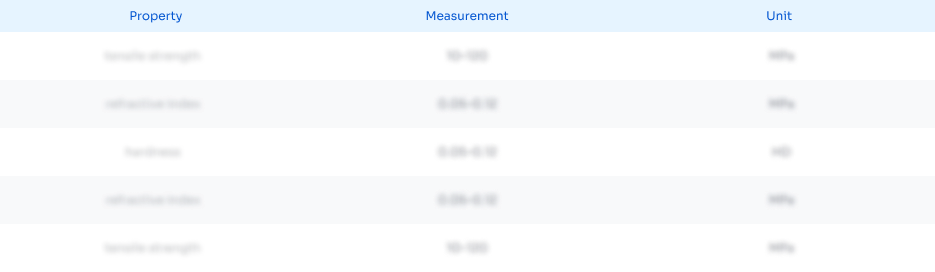
Abstract
Description
Claims
Application Information

- Generate Ideas
- Intellectual Property
- Life Sciences
- Materials
- Tech Scout
- Unparalleled Data Quality
- Higher Quality Content
- 60% Fewer Hallucinations
Browse by: Latest US Patents, China's latest patents, Technical Efficacy Thesaurus, Application Domain, Technology Topic, Popular Technical Reports.
© 2025 PatSnap. All rights reserved.Legal|Privacy policy|Modern Slavery Act Transparency Statement|Sitemap|About US| Contact US: help@patsnap.com